The Problem
Plastics are used extensively within the logistics sector for a variety of reasons such as durability, cost effectiveness and malleability. Its usage has surged to unprecedented levels, with packaging materials accounting for 36% of global plastic consumption. Alarmingly, 85% of this plastic waste remains unmanaged.
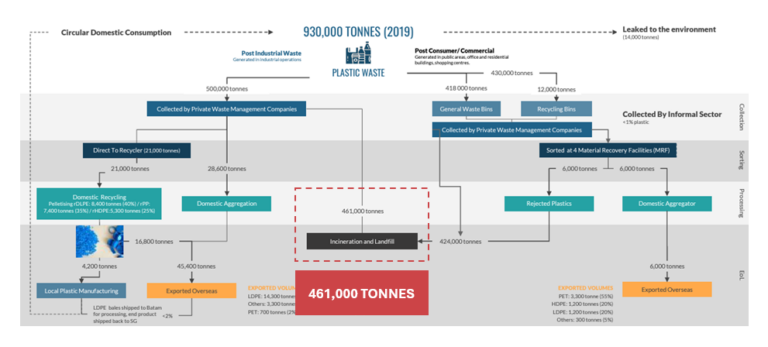
In Singapore, around 930,000 tonnes of plastic waste is generated each year, and 461,000 tonnes of waste generated in industrial operations is not recycled.
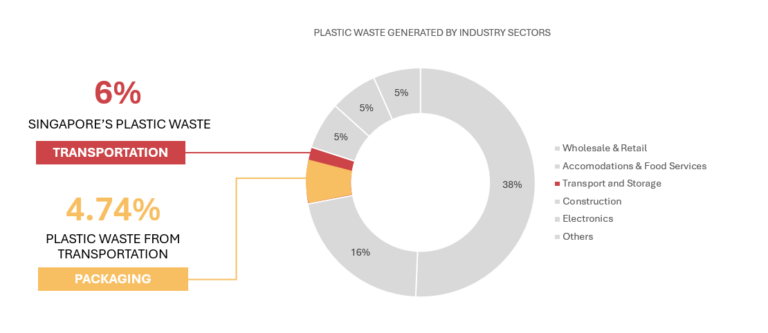
Transportation accounts for 6% of the country’s plastic waste, with packaging from transportation alone comprising 4.74%.
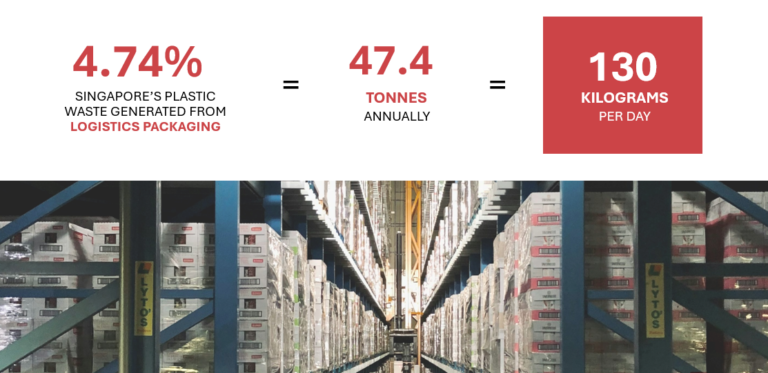
This 4.74% of plastic waste translates to approximately 47.7 tonnes of plastic waste annually, meaning 130 kilograms per day.
ENVIRONMENTAL CONCERNS
Negative impact of plastic on health and the environment
DB SCHENKER RED LION FACILITY
DB Schenker is a global logistics provider offering air, land, sea freight, and contract logistics services. The company in collaboration is particularly the Red Lion facility in Singapore, which is a mechanised air freight hub, packing and transporting build-up packages via air. Due to the nature of its operations as a logistics company, it relies heavily on plastic use.
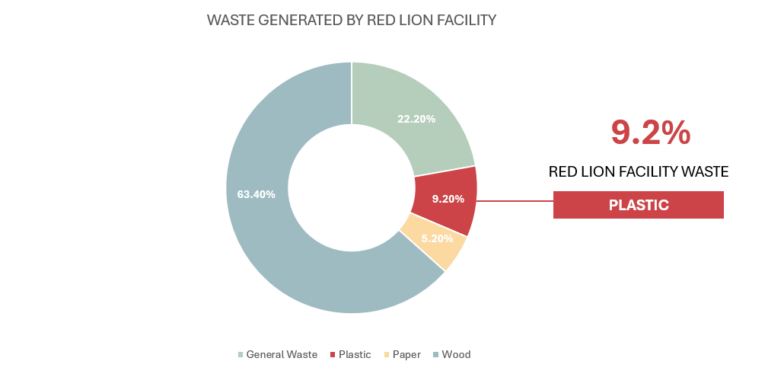
To counter this heavy use of plastic, the company is going towards more sustainable logistics and have come up with a strategic framework comprising three dimensions namely Clean Logistics, Thriving Workplace and Trusted Supply Chain.
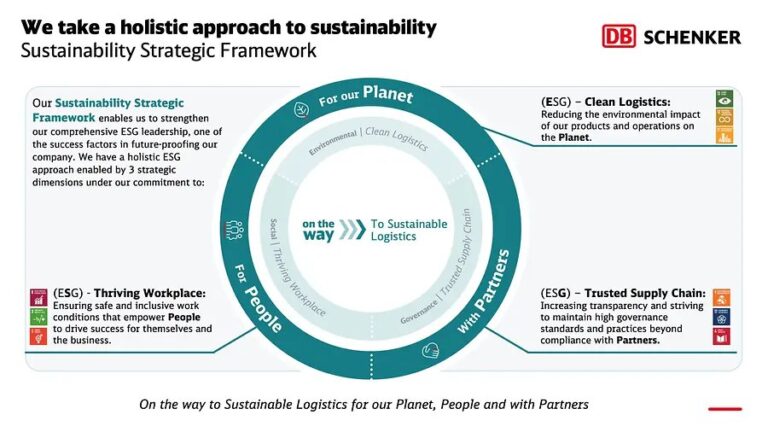
- 1. Investing in low-carbon freight solutions
- 2. Improving resource efficiency in warehouses
- 3. Establish sustainable supply chains
- 4. Forging new partnerships to create a circular economy
In an era marked by globalisation and high levels of pollution, how can we contribute to building a sustainable economy within the logistics sector?
Introducing
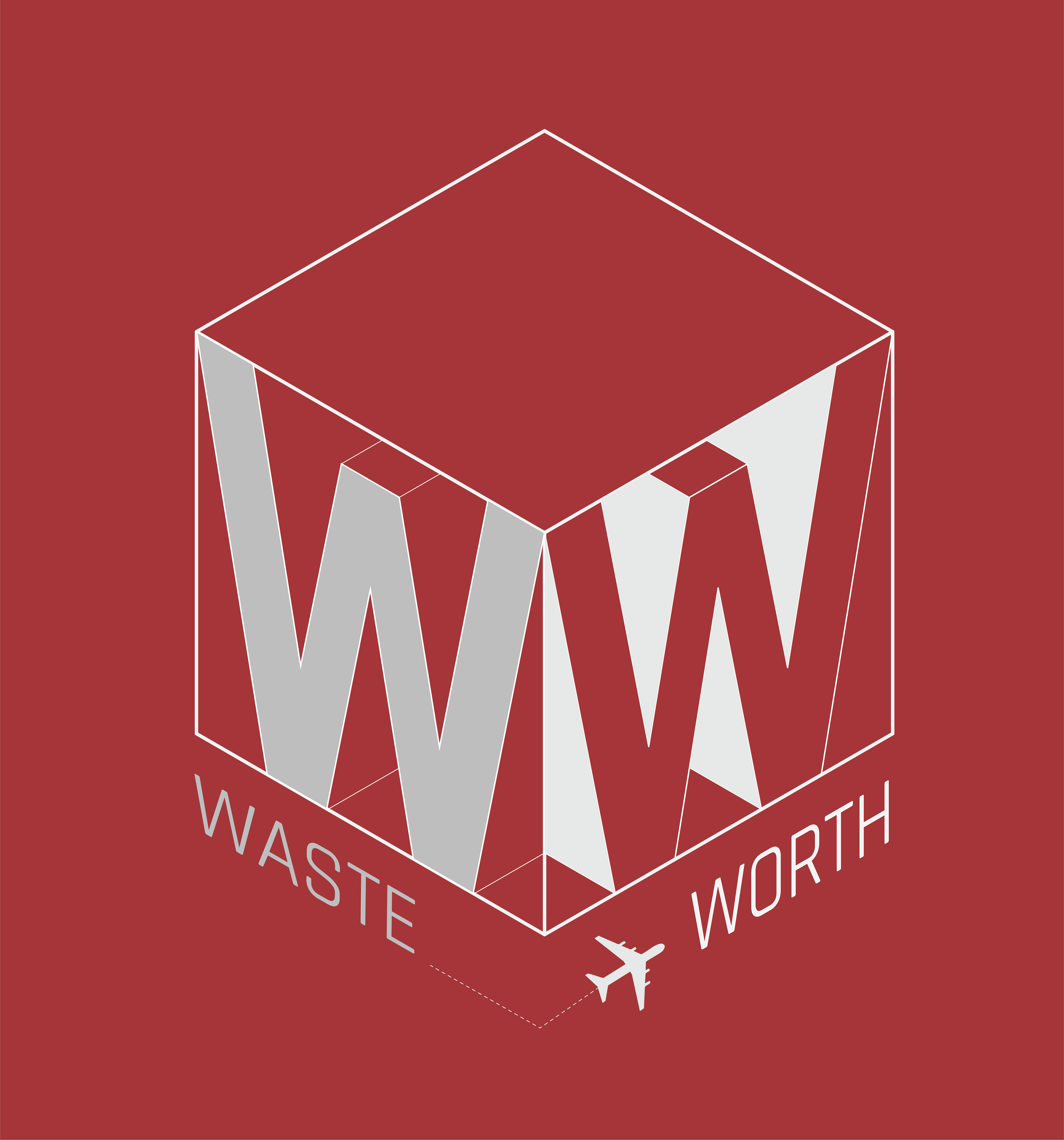
WASTE TO WORTH
Transforming Plastic Waste into Logistics Solutions
To support the DB Schenker’s sustainability goals by designing custom solutions using plastic waste materials found in Red Lion’s operation (LDPE, LLDPE) to reduce wastage of materials such as styrofoam blocks and cardboard angle bars used exclusively in air freight operations, thereby reducing material consumption by 1% annually and advancing a circular economy.
Proposed Solution
Our proposed solution consists of two parts; designing custom solutions for the Red Lion Facility as well as establishing a relationship with recycling companies to outsource the recycling process
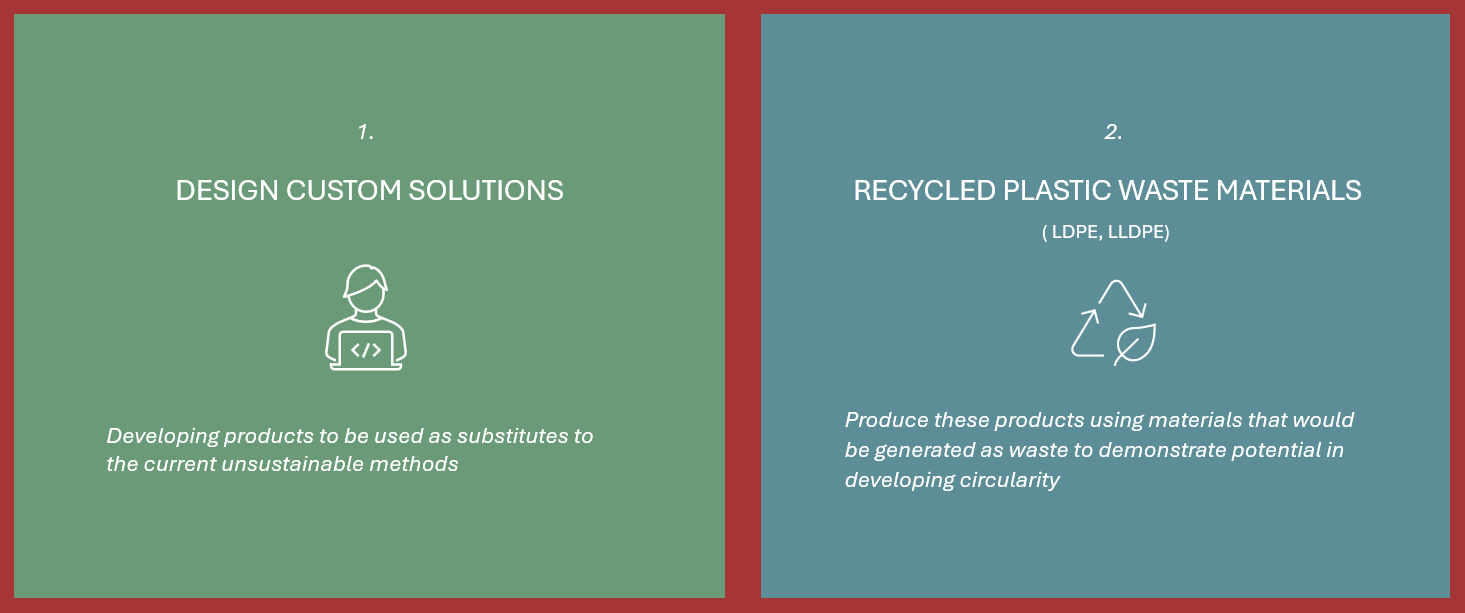
This two-part process then allows for a circular economy to be established within the facility, making their operations sustainable and self-sufficient
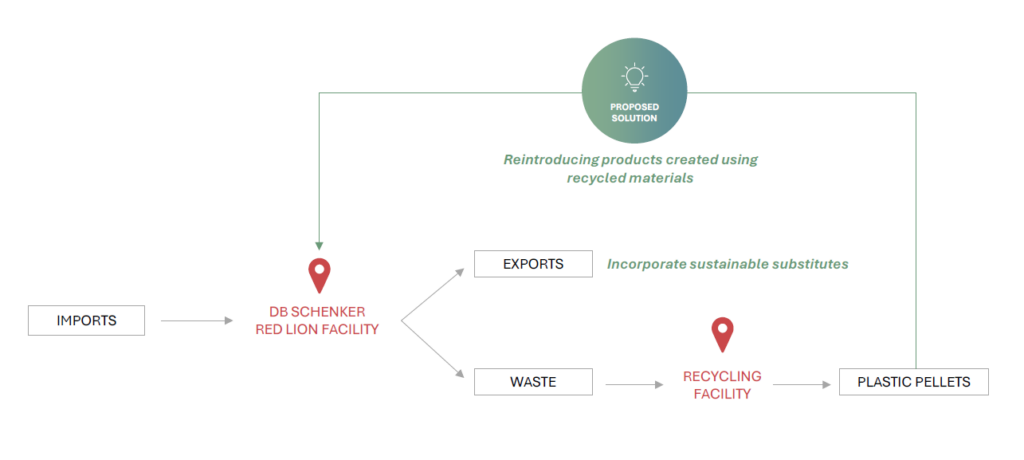
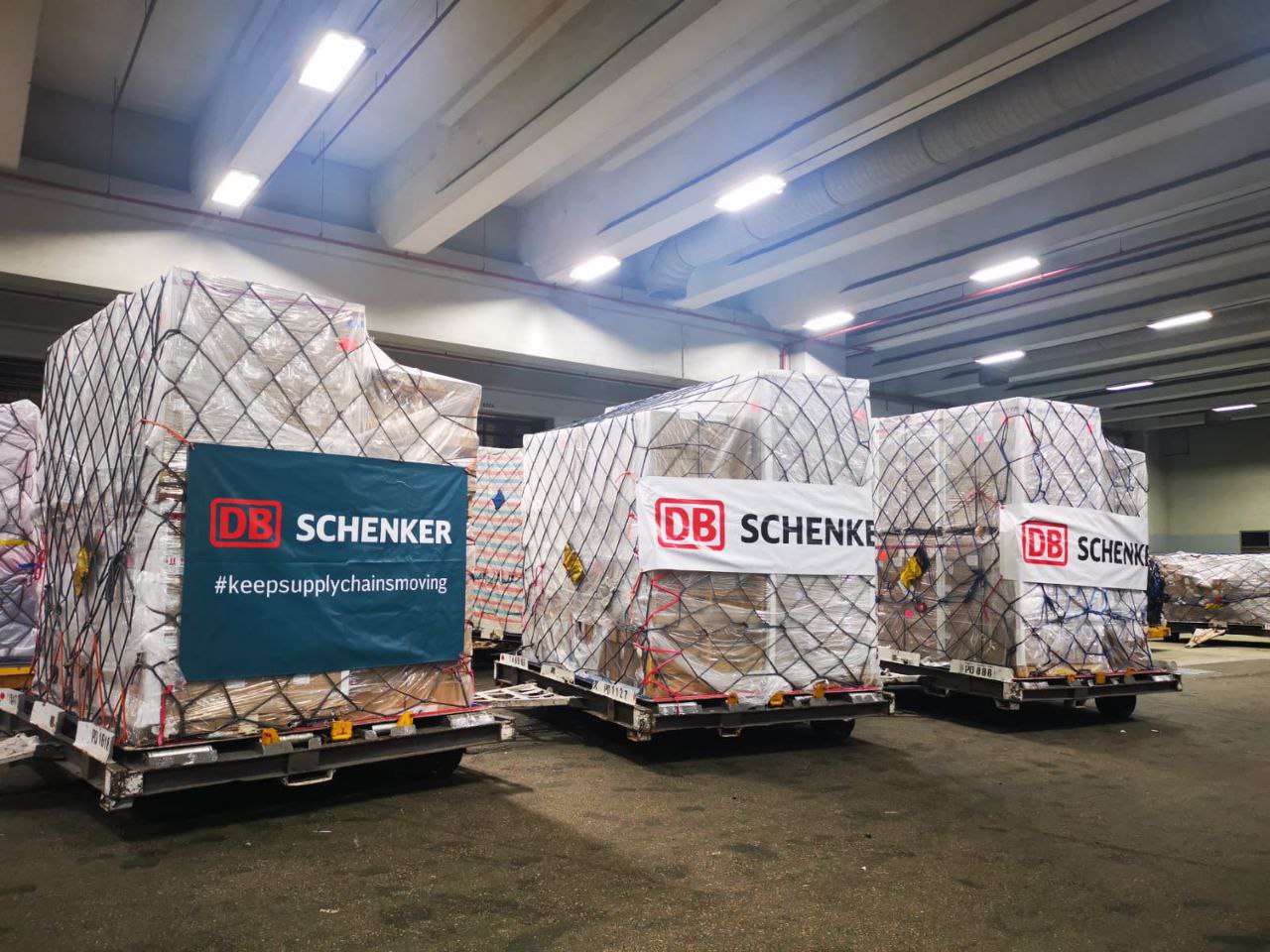
Company Operations
Site visits were conducted to better understand the facility’s operations of import break-down and package export build up. The sources and types of waste generated, as well as their recycling potential were identified. Surveys were also carried out with workers to understand work inefficiences.
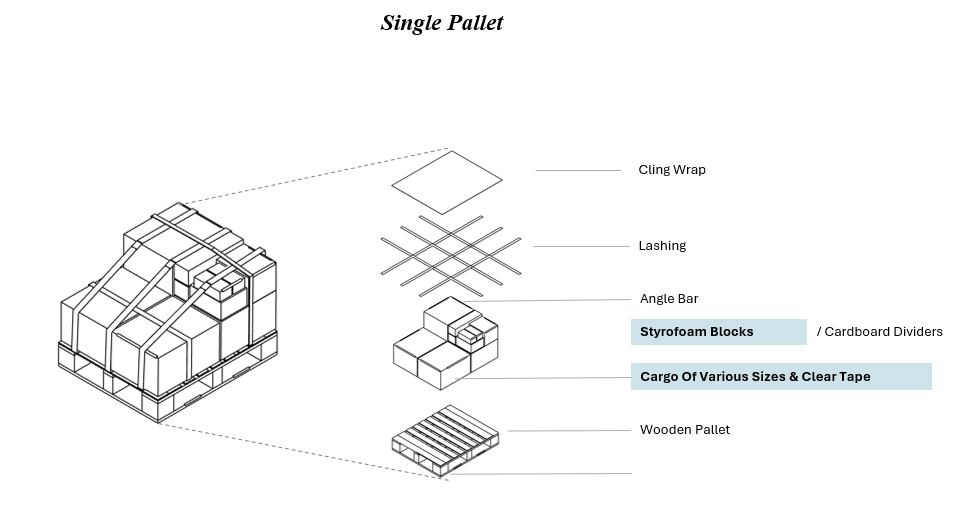
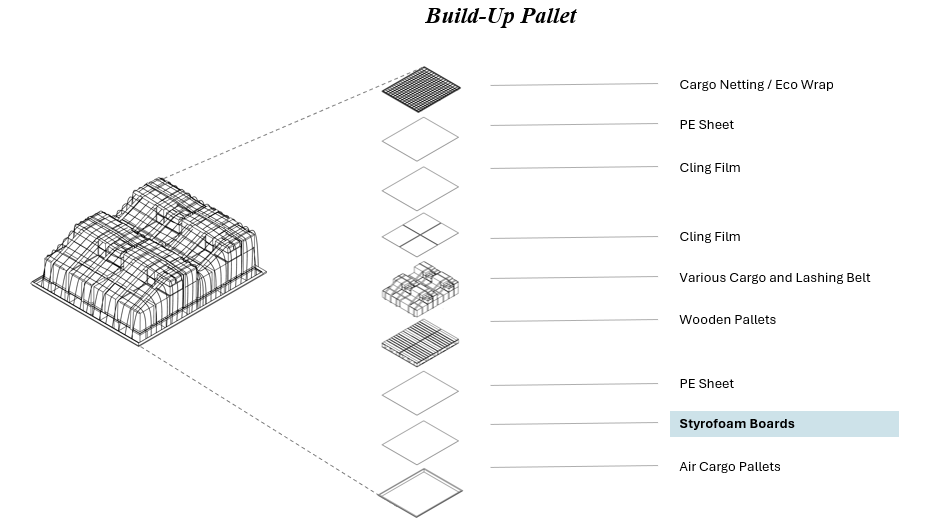
The facility packs the individual packages into single pallets and a few of these pallets then form the Build-Up Pallet as shown in the two diagrams.
MATERIAL ANALYSIS
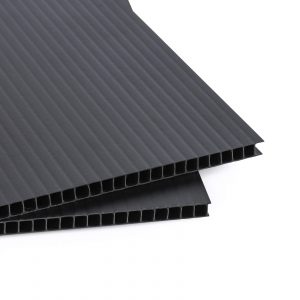
Corrugated Board
Corrugated Board
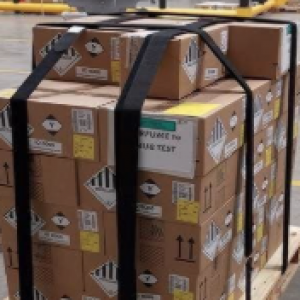
Strapping Band
Strapping Band
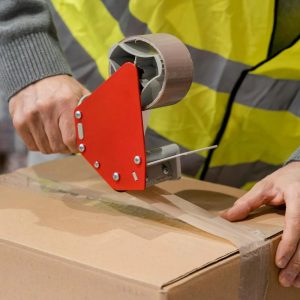
Clear Tape
Clear Tape
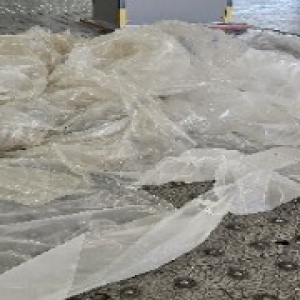
PE Sheet
PE Sheet
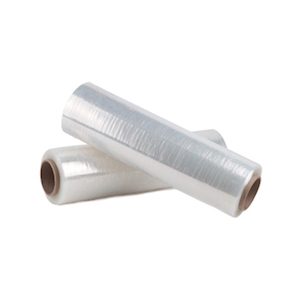
Shrink Wrap
Shrink Wrap

Styrofoam
Styrofoam

Pallets
Pallets
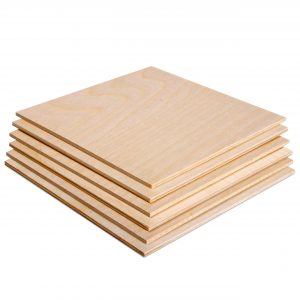
Plywood
Plywood
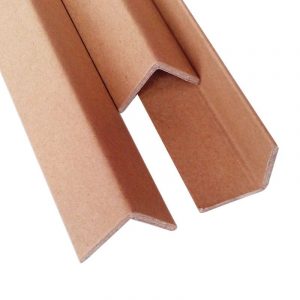
Angle Bar
Angle Bar
OUR SCOPE
Waste generated from exports will not be considered for recycling as they are not collected within the facility.
The materials collected from imports are as follows:
- Shrink Wrap
- Clear Tape
- PE Sheets
- Strapping Band
- Corrugated Sheets
- Wooden Pallets
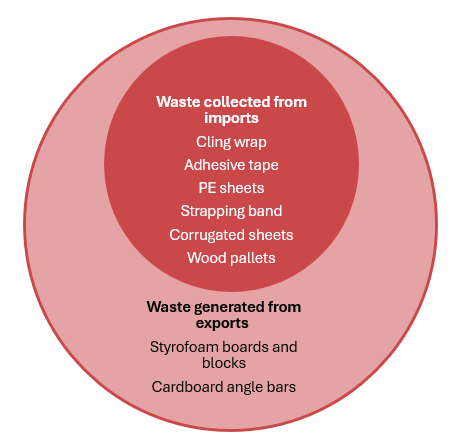
We then further analysed and narrowed down two products that will be within our scope to be recycled into pellets: PE Sheets and Cling Wrap, which happens to be made of LDPE plastic.
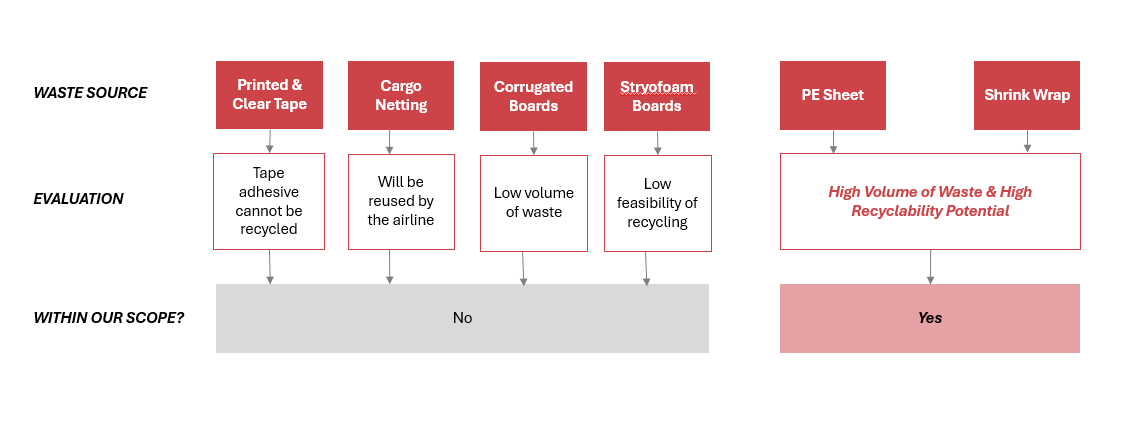
Based on the site survery, the most bought, used and wasted materials are as shown below:
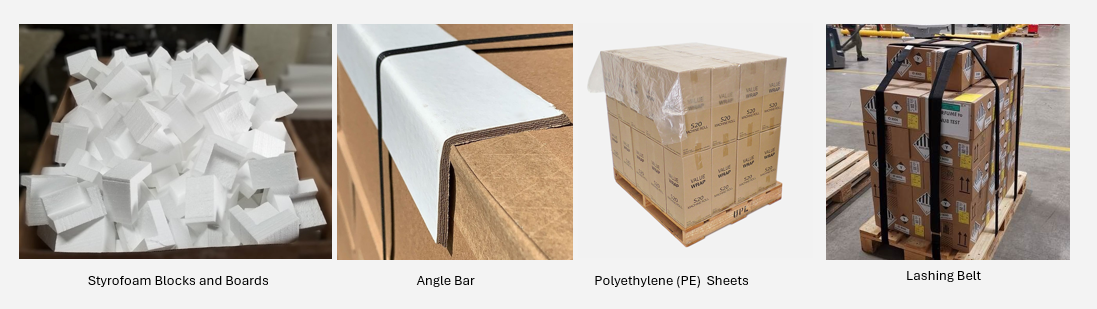
The products were thoughtfully designed to replace the most commonly used and frequently discarded items, serving the same functions while promoting sustainability. This approach supports the creation of a circular economy within the facility by reducing waste and encouraging resource reuse.
PRODUCTS
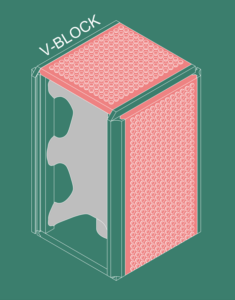
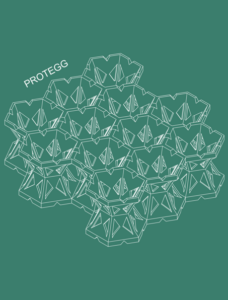
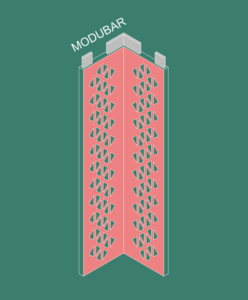
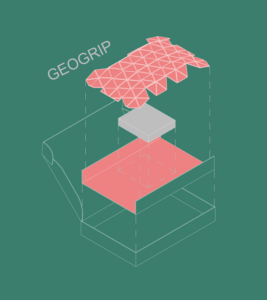
V-BLOCK
V-Block serves as an additional support for pallets carrying heavy loads, offering a structurally optimised alternative to conventional Styrofoam blocks. Utilising generative design principles, it enhances strength while minimising material usage. Its innovative Velcro-inspired attachment system improves stability and ease of use, allowing for quick and secure assembly in various logistics applications.

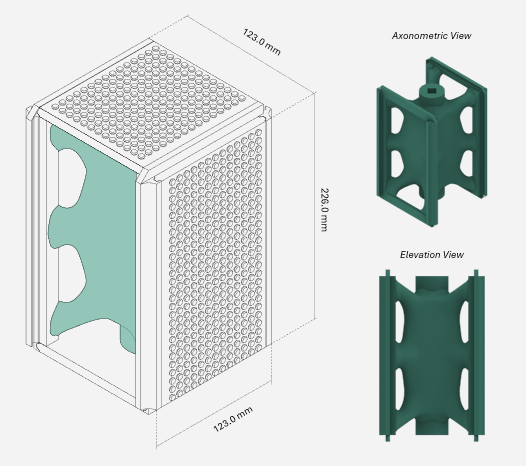
Artificial Intelligence Generated Core
Generative design was utilised in the design iterations of the core structure to maximise strength, while simultaneously minimising material usage and thus, minimising weight.
This essential step ensures Waste to Worth’s products are comparable or better in terms of strength to weight ratio in comparison to the Styrofoam block, and thus, a significantly more attractive substitute to potential users.
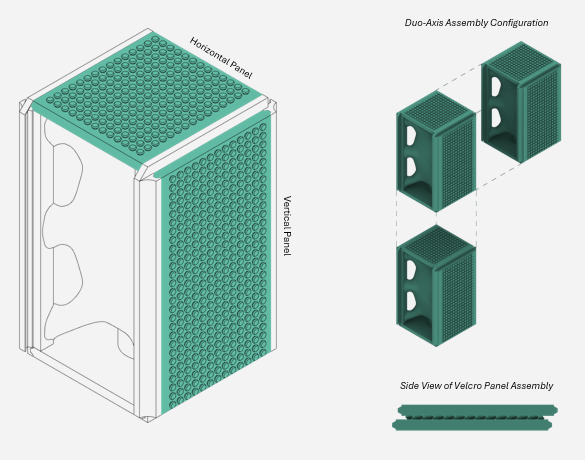
Vertical and Horizontal Velcro Panels
A notable feature of this design is the use of Velcro, which provides a secure hold while allowing for easy detachment. This eliminates the need for traditional fastening methods such as screws, magnets, or adhesives.
Additionally, the system is both durable and reusable, offering a sustainable alternative. Its design is also easily scalable, making it adaptable to various applications and sizes.
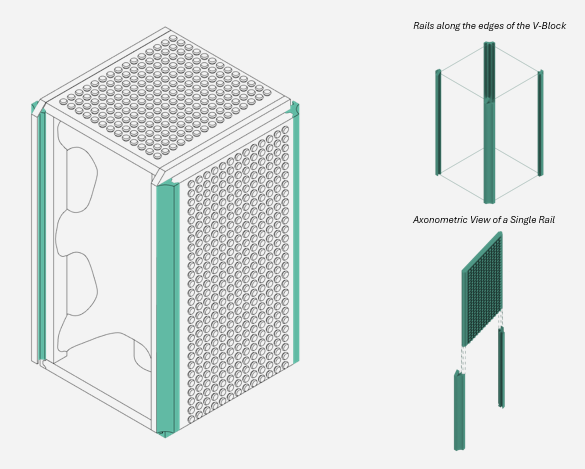
Vertical and Horizontal Sliding Rails
To enhance the longevity and ease of maintenance of the system, sliding rails were integrated into the design to hold the 3D – printed Velcro components .
This modular feature allows the Velcro to be easily removed and replaced if they become worn, damaged or lose their grip strength over time
By avoiding throwing away the entire structure, the sliding rail mechanism significantly improves the efficiency of maintenance and reduces material waste
Separation of the Core and Velcro
The blocks can be used without the velcro panels as well and serves the same purpose of giving the wooden pallets additional supports.
This also helps with reducing the weight of the blocks if multiple blocks are not needed to be connected
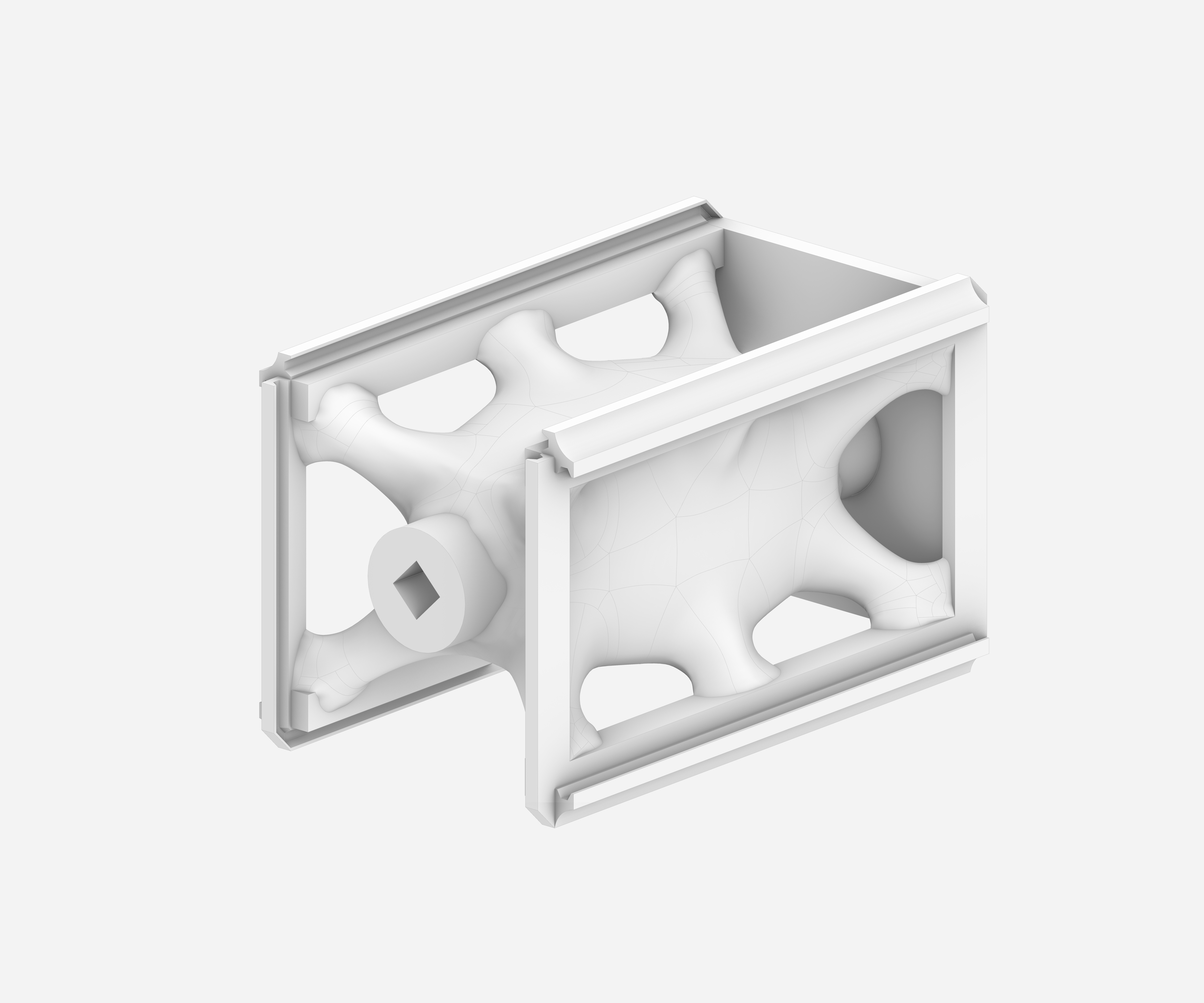
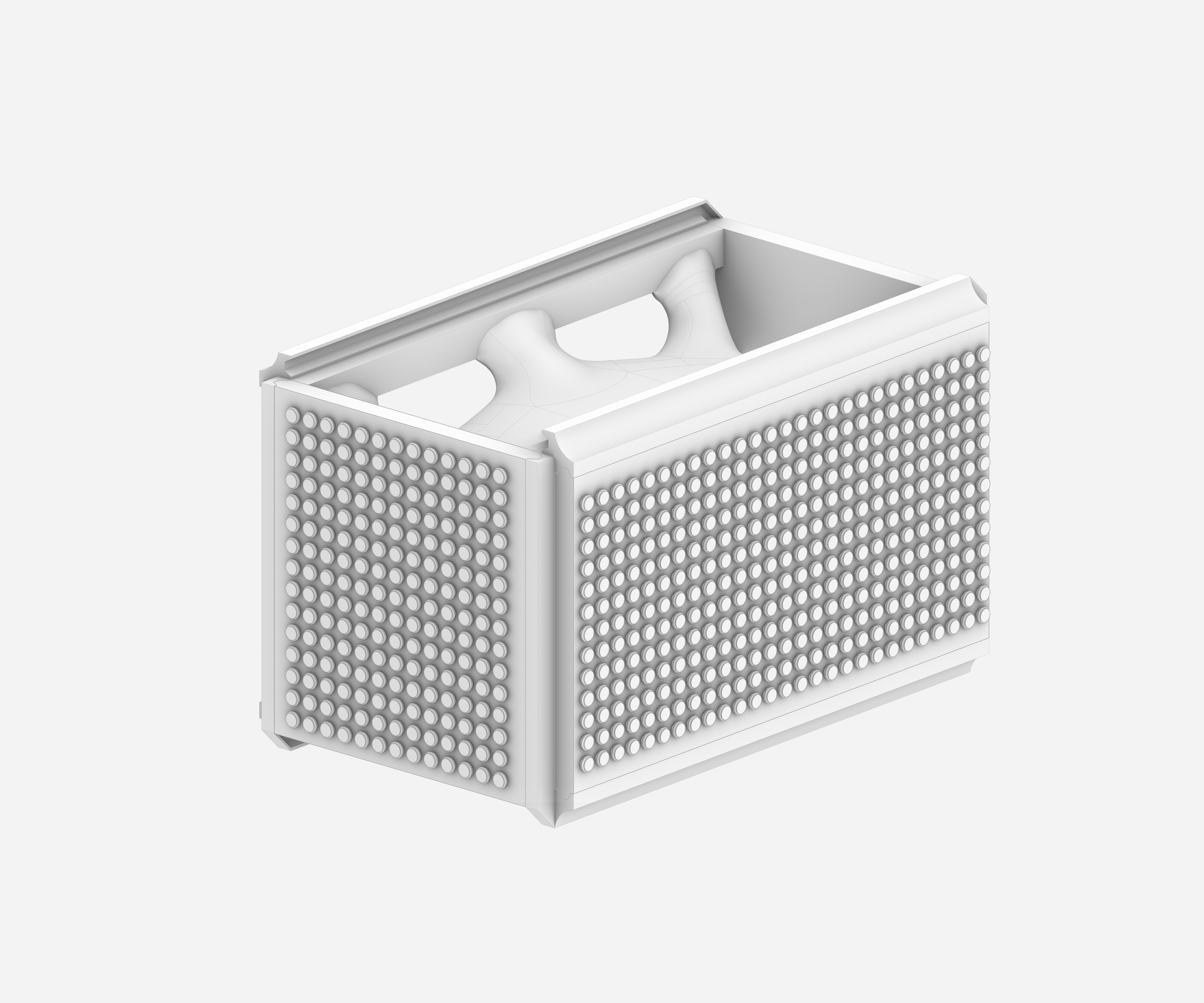
PROTEGG
ProtEgg is designed to elevate pallet platforms to meet international shipping standards and serve as infill for packaging, ensuring secure fastening and minimising damage. Its egg carton-inspired design optimises the strength-to-weight ratio through strategic material removal, maintaining structural integrity while reducing material use.
Additionally, it is designed as a strong, modular unit that comes in 3 different sizes which cater to the different uses of styrofoam boards. This includes being placed between boxes to provide additional padding and protection, in addition to elevating the build-up pallets off the base plate.
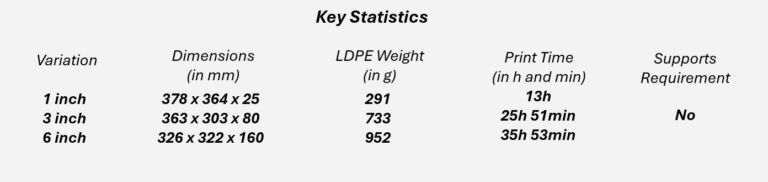
1″ HEIGHT
3″ HEIGHT
6″ HEIGHT

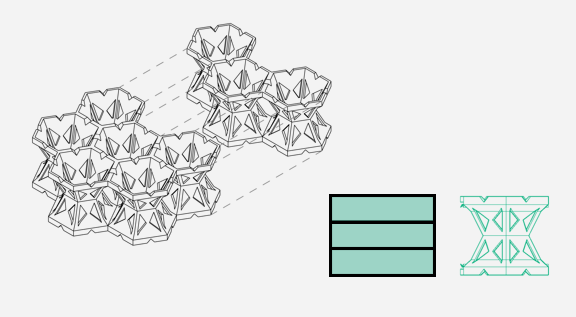
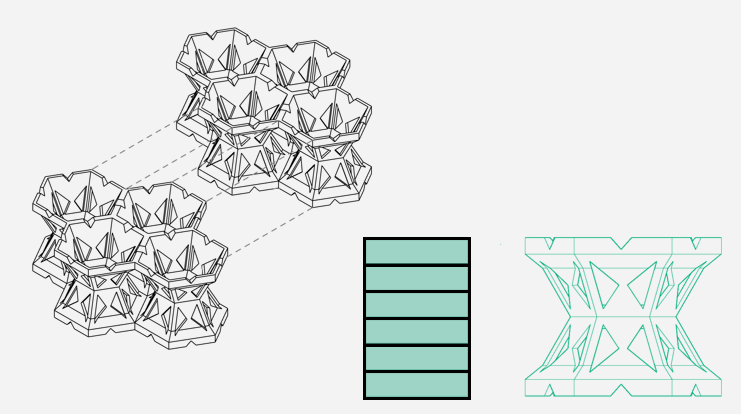
- Matches the dimension of the currently used Styrofoam boards, used to slot vertically between boxes
- Is stacked twice to match the 6-inch height raising requirement of the BUP, while being more efficient to print than 6-inch variant
- Is able to raise the height of the pallet to meet BUP requirements
Skeletal Design & Attachment Clip
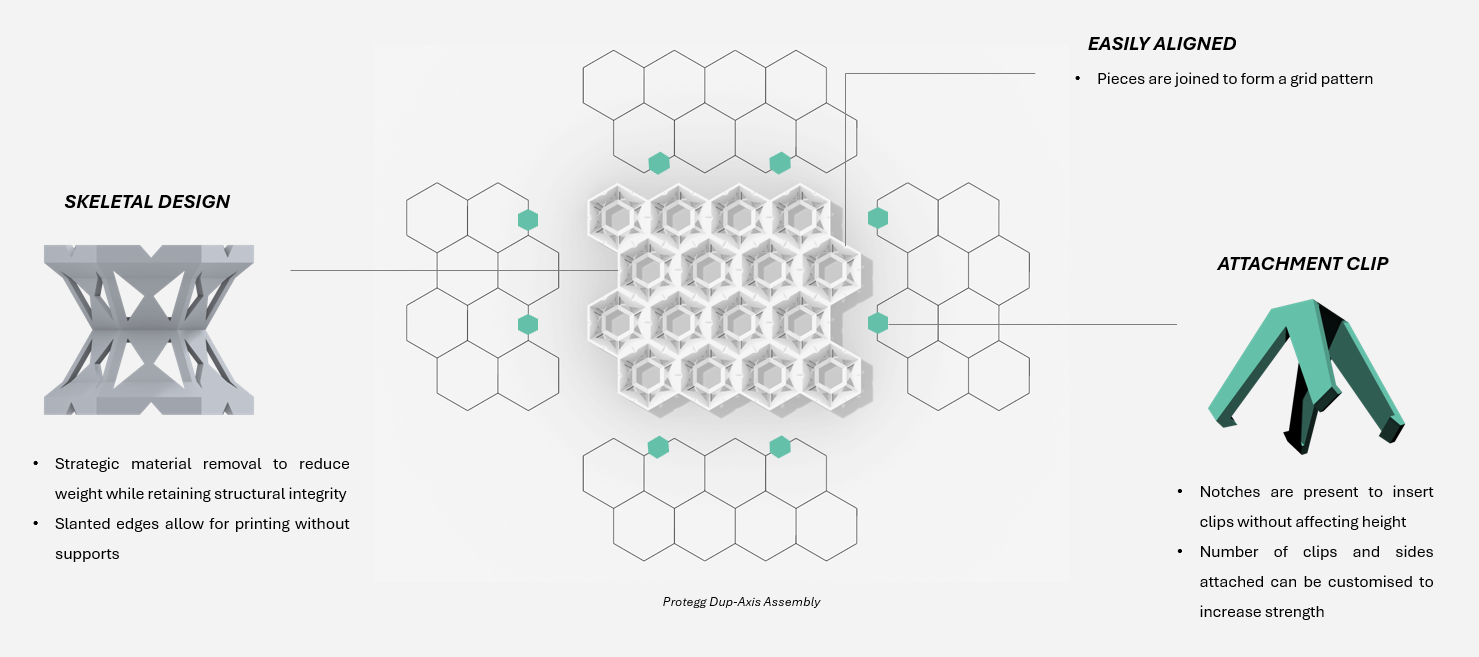
Attachment of Modular Pieces
The design consists of several individual pieces that can be combined using clips to achieve the desired size.
This modular approach allows for flexibility and customization based on specific needs or applications.
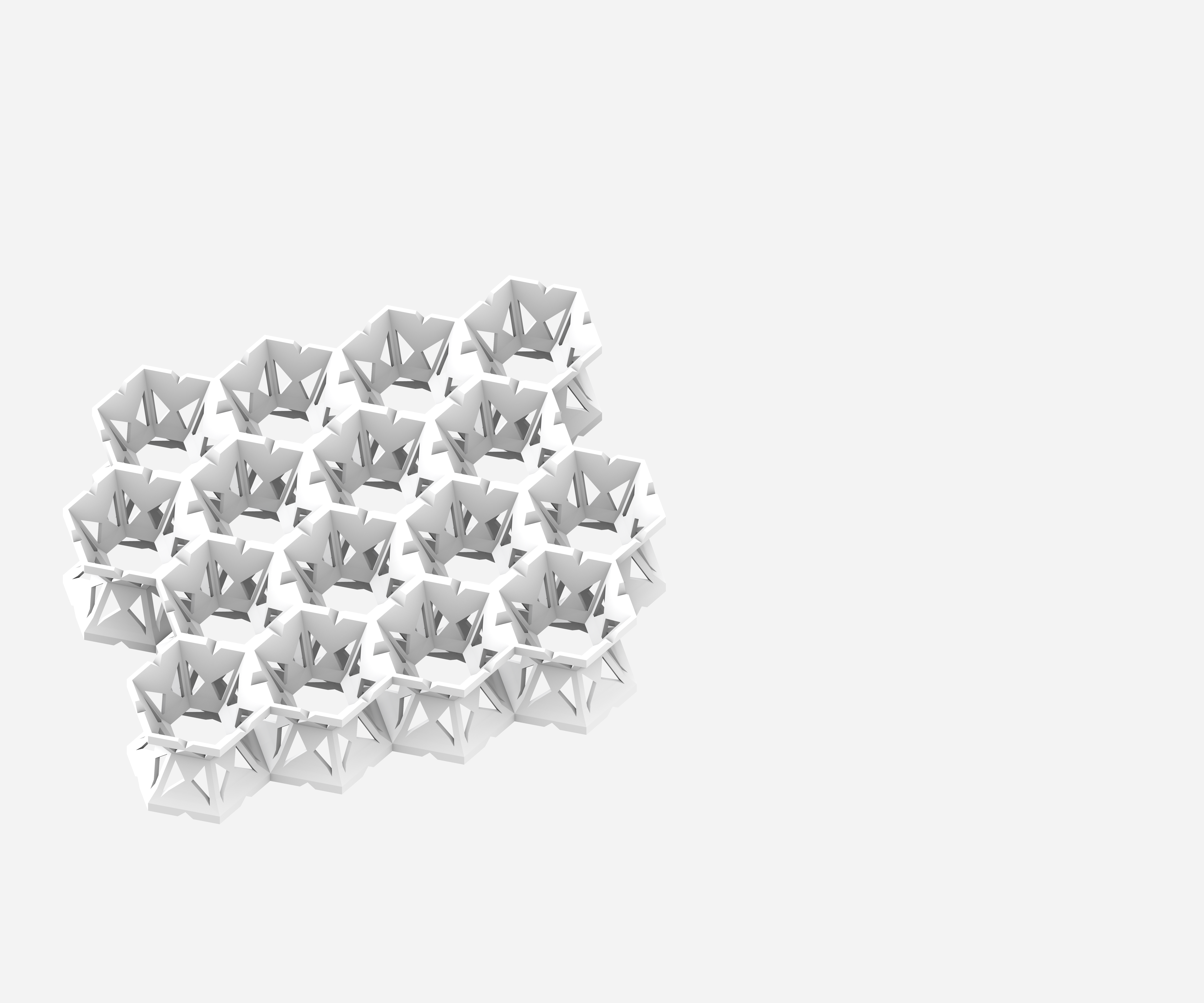
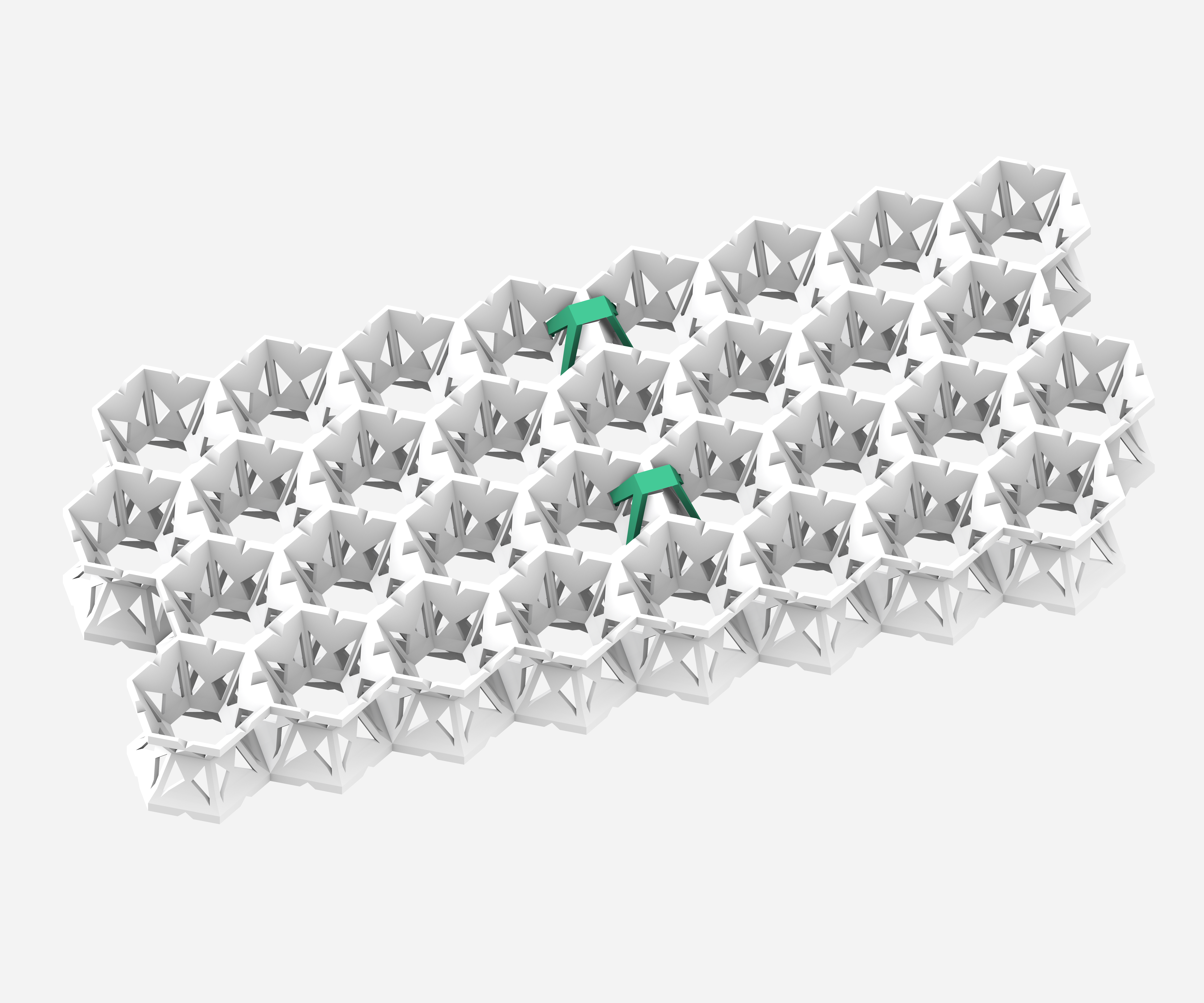
MODUBAR
ModuBar is an innovative alternative to the currently-used cardboard angle bars, coming in modular pieces which can protect box edges of any size. The triangular pattern maximises strength while minimising material and weight.

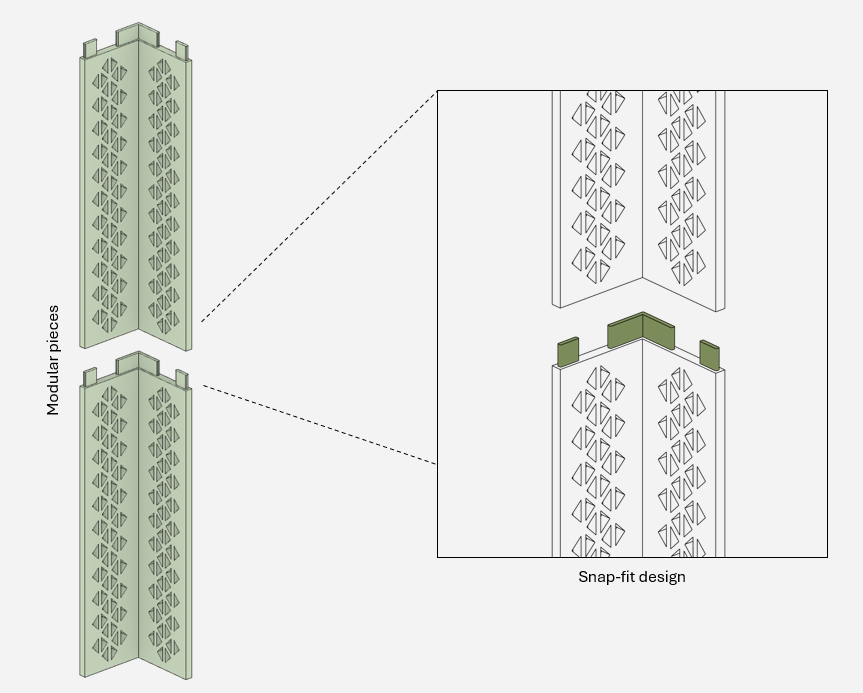
Modularity - Snapping Pieces
The snap-fit design enables the creation of angle bar pieces with variable lengths, allowing them to be easily adjusted to fit different box sizes.
This versatile feature ensures compatibility with a range of dimensions, enhancing the overall adaptability of the system.
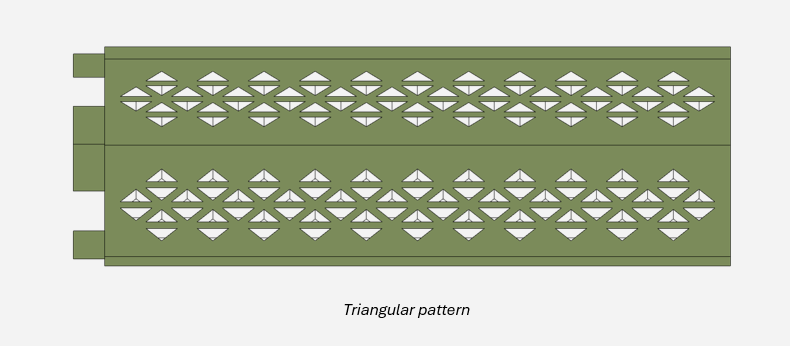
Triangular Pattern
The triangular design pattern is used to maximize both strength and protective surface area while minimizing the amount of material required for the angle bar.
This efficient geometry enhances durability without compromising on resource efficiency.
GEOGRIP
GeoGrip is an innovative approach to internal packaging, by securing goods in place to ensure that products are not damaged during transportation. Its flexible triangular mesh allows it to cater to a wide variety of products while maintaining its protective structure. It is a two-piece product with the mesh and base piece.

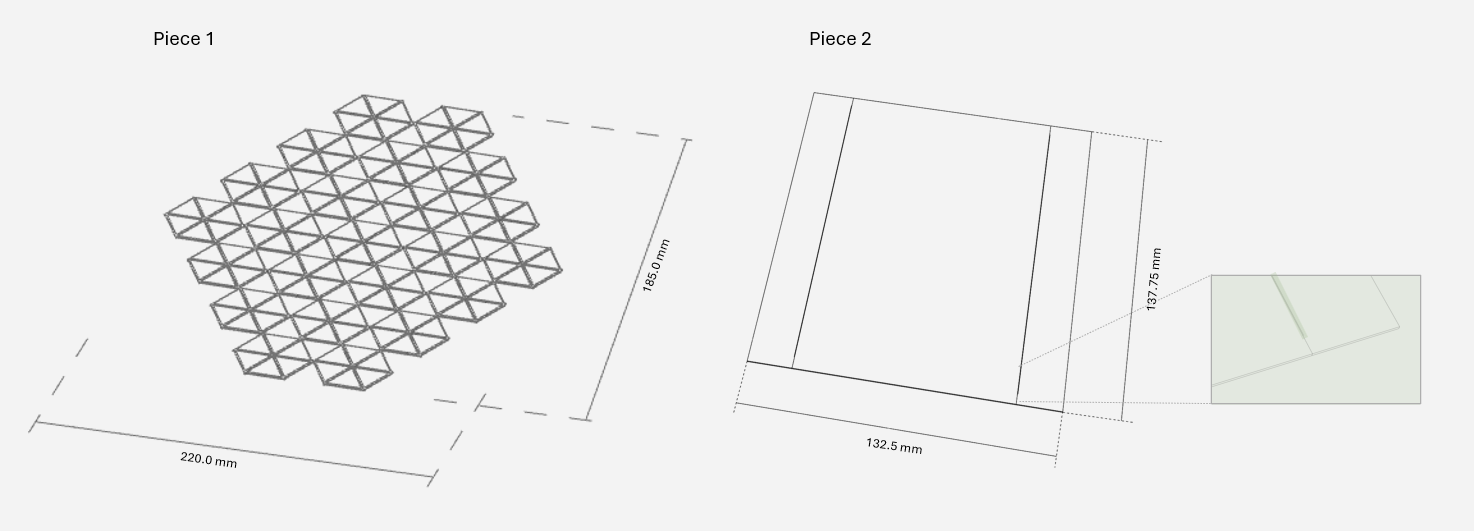
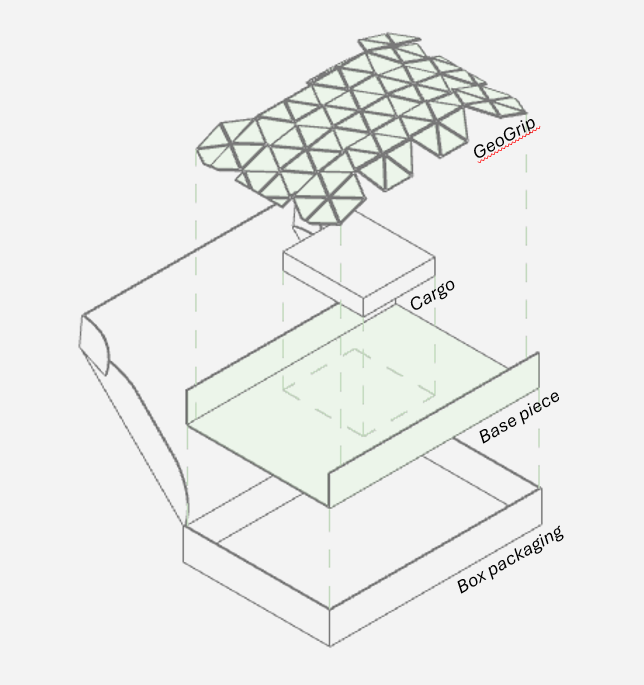
Modularity - Snapping Pieces
Notable features of the mesh design include its thin and flexible structure, which allows it to conform to the shape of various types of cargo, securely fastening them in place.
The hexagonal grid pattern supports an easily scalable design, enabling the creation of larger or smaller mesh variations as needed.
Additionally, a base piece is integrated into the system, allowing the mesh to be locked securely into position for enhanced stability.
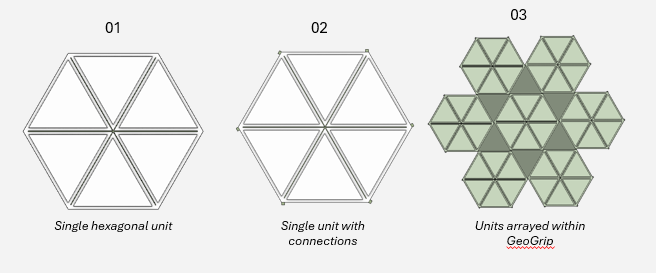
Hexagonal Structure
The design features a single hexagonal unit with a central slit to increase permeability. Connectors are positioned at each corner, allowing multiple units to be joined together.
When arrayed, the units form a pattern with triangular gaps between them, enhancing both flexibility and connectivity.
How are these products used within the Build Up Pallet?
Pellet Extruder Modification
Instead of converting LDPE pellets into filament for 3D printing, the printer was modified to directly accept the pellets. An extruder was attached to the printer, allowing it to process the raw material without the need for filament conversion.
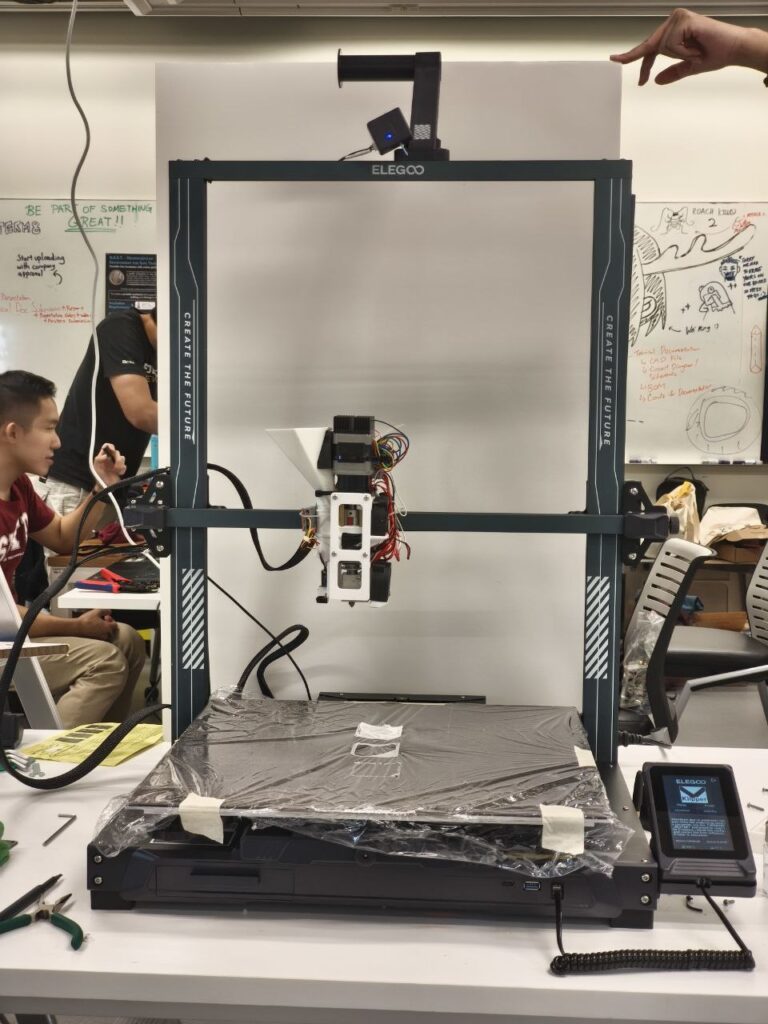
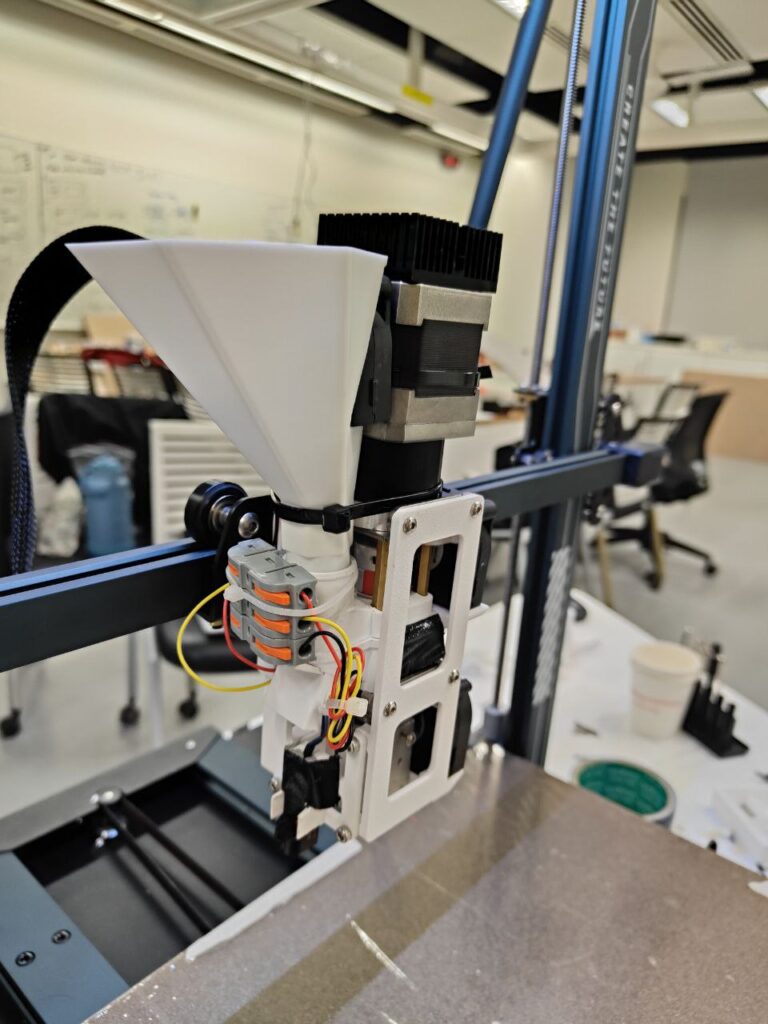
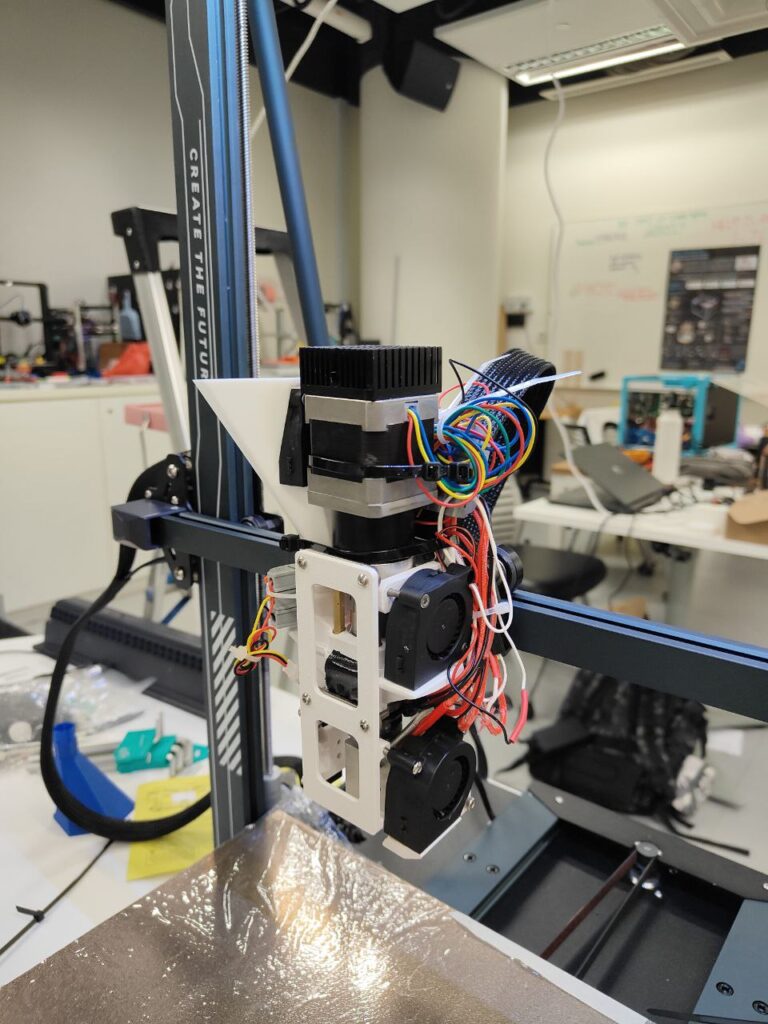
Exploded View of Extruder
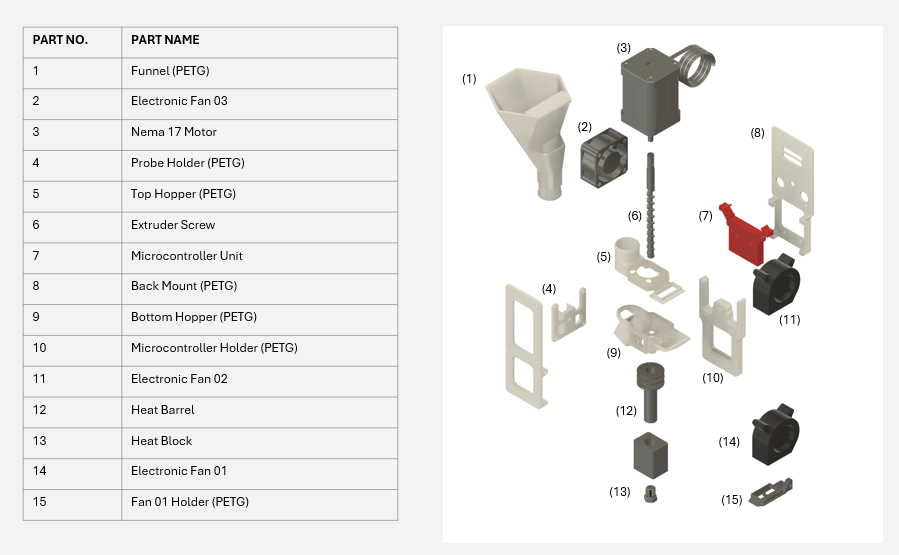
The Printer in Action
The LDPE pellets are heated and melted to create a continuous flow of material that feeds directly into the modified 3D printer.
This eliminates the need first to convert the pellets into filament, streamlining the production process. By integrating a custom extruder, the printer is able to handle the raw pellets efficiently, enabling on-site recycling and transforming waste material into new, functional products.
This approach not only reduces processing time and costs but also supports a more sustainable and circular manufacturing system.
Collective Circular Economy
The modification of the 3D printer, combined with the replacement of single-use items with products printed from recycled LDPE, plays a key role in fostering a circular economy within the facility.
By turning waste into functional, reusable items on-site, this system reduces dependency on new materials, minimizes waste generation, and promotes sustainable resource management throughout the production cycle.
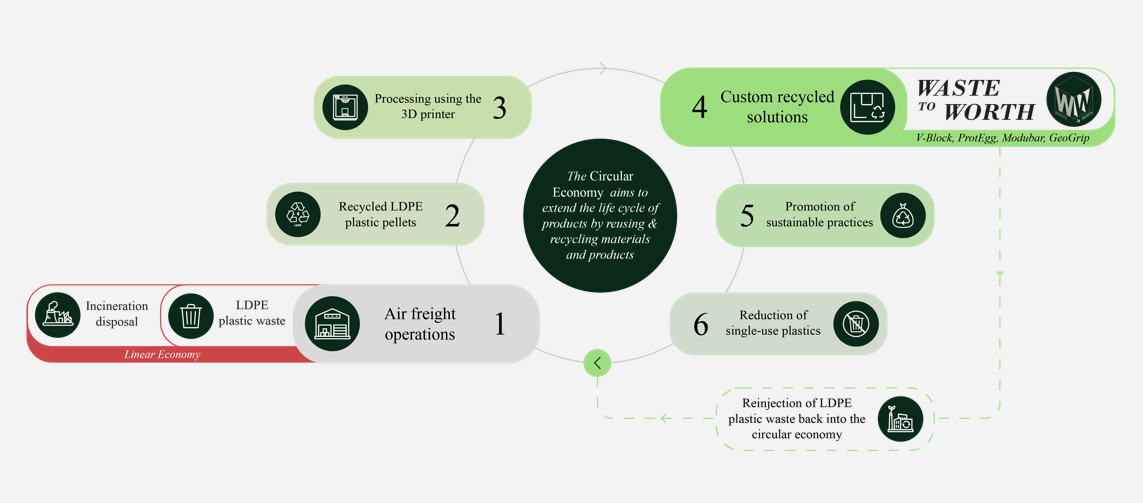
Project Goals
Gallery
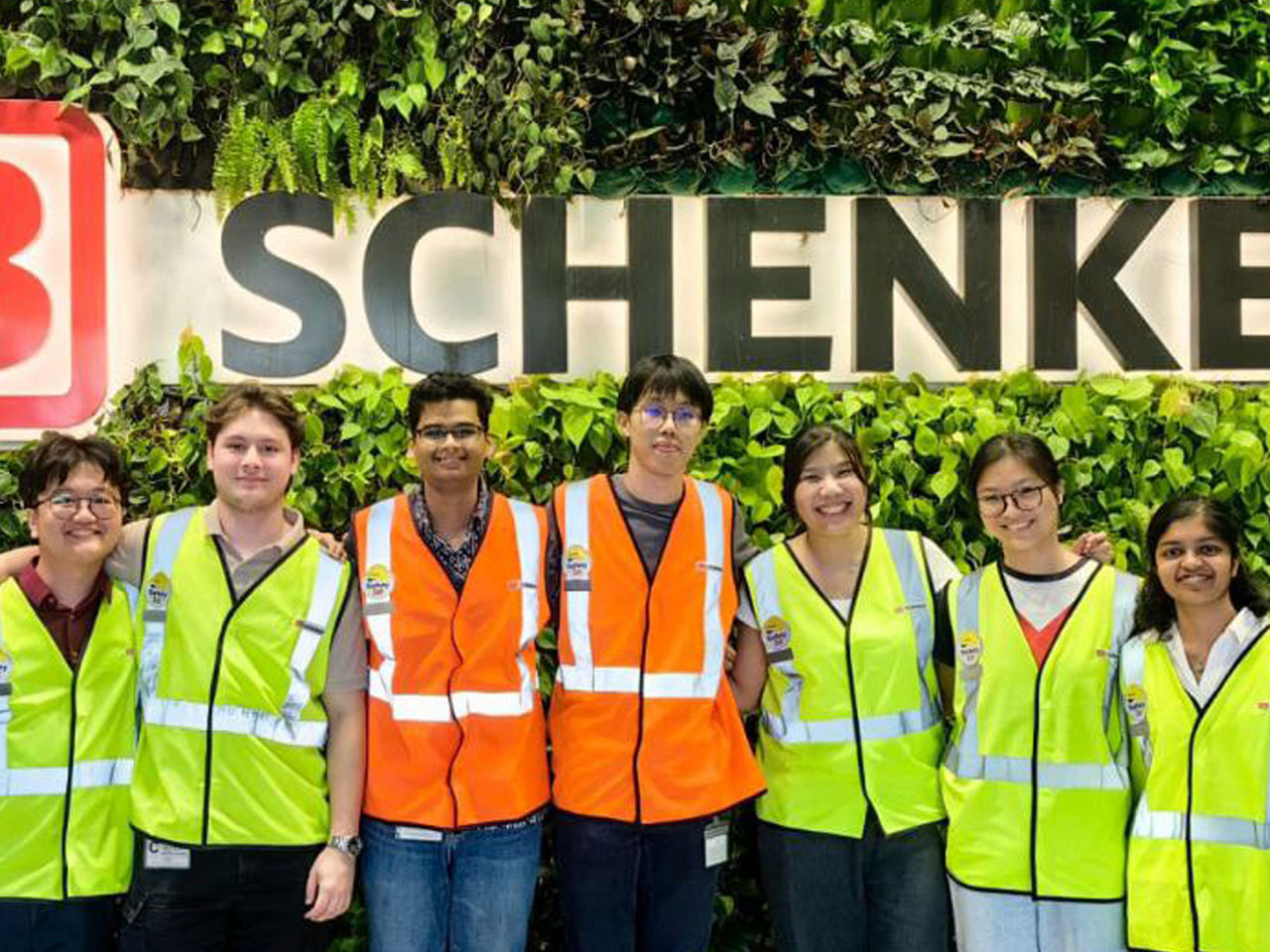
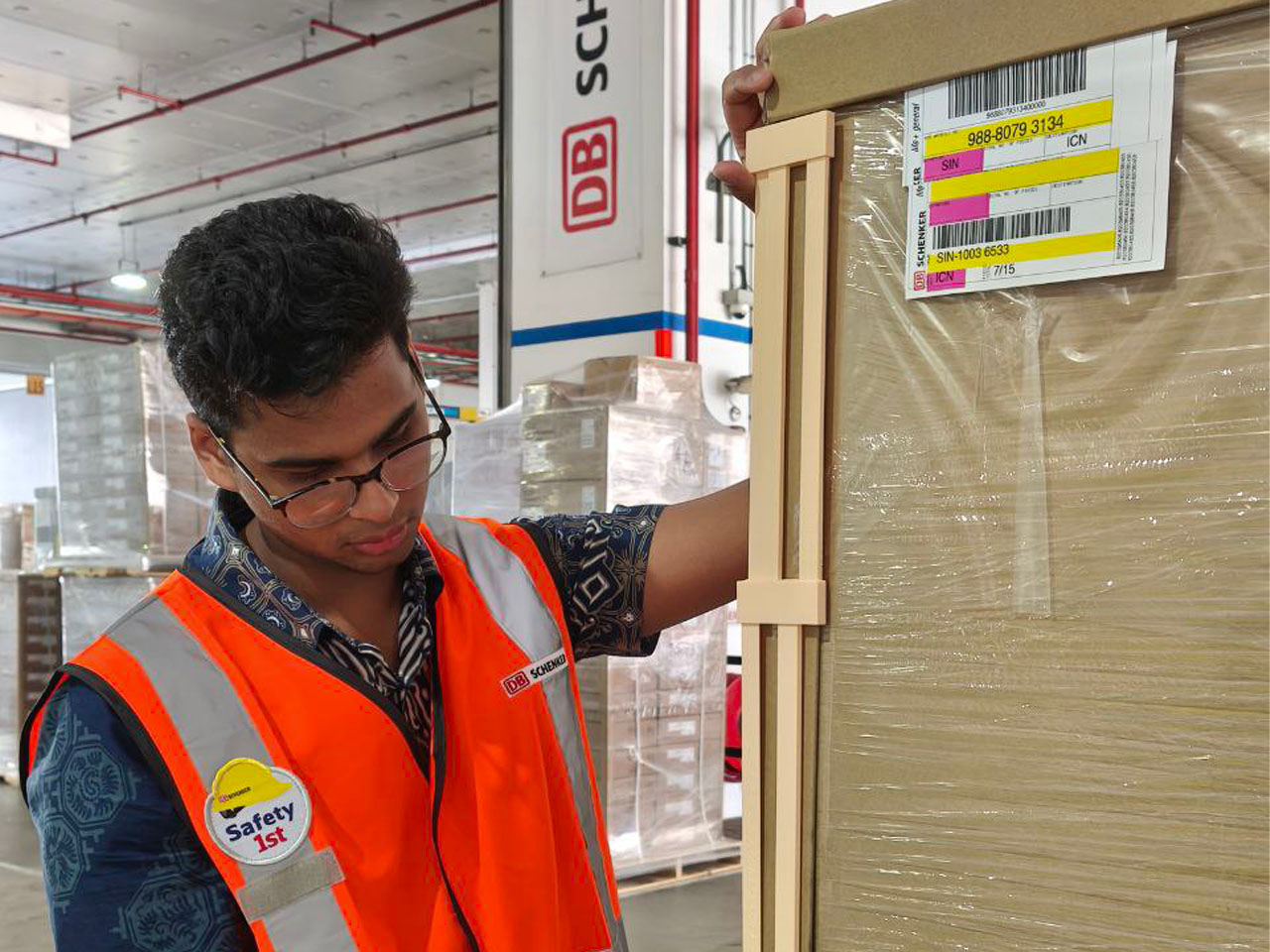
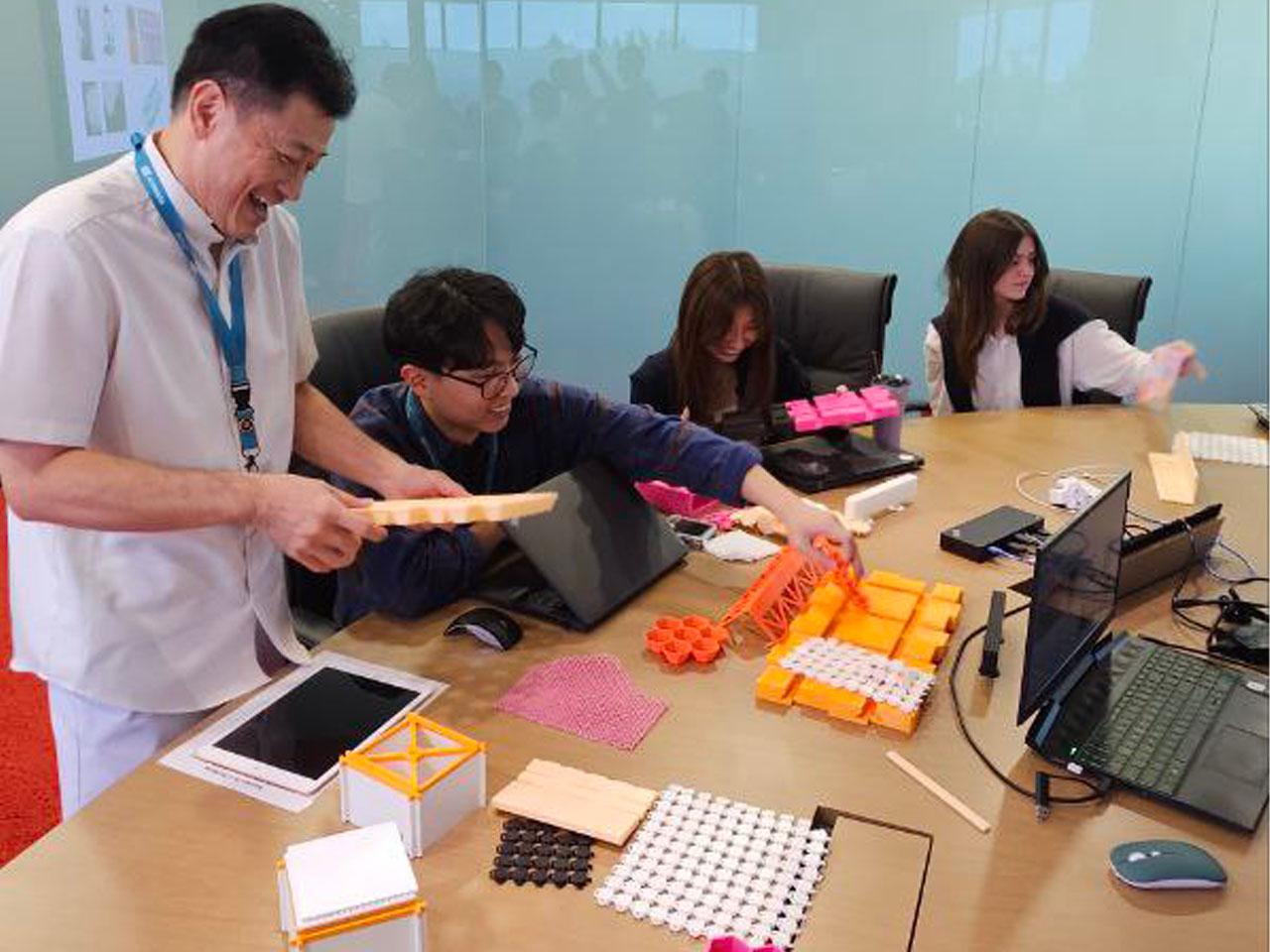
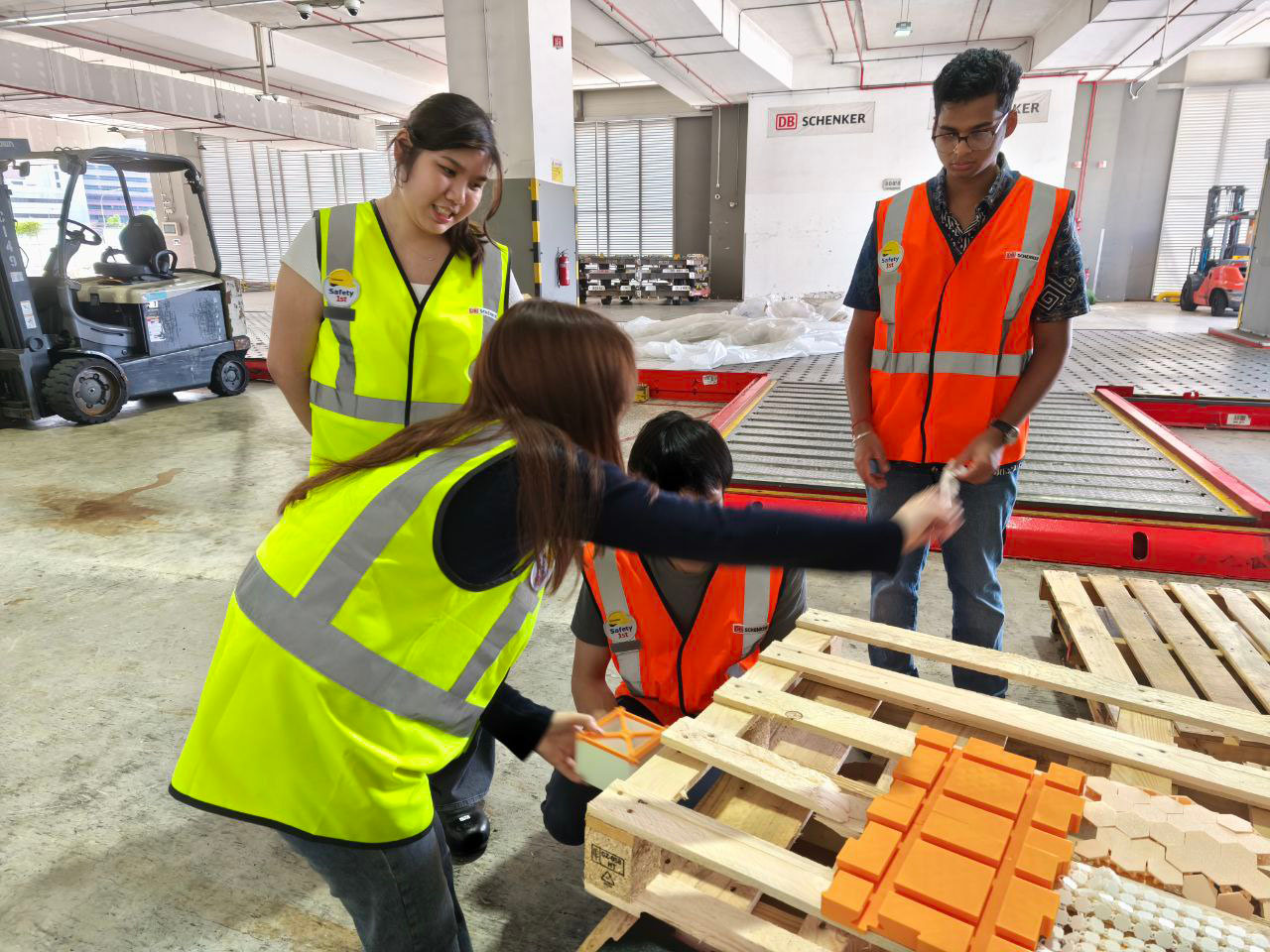
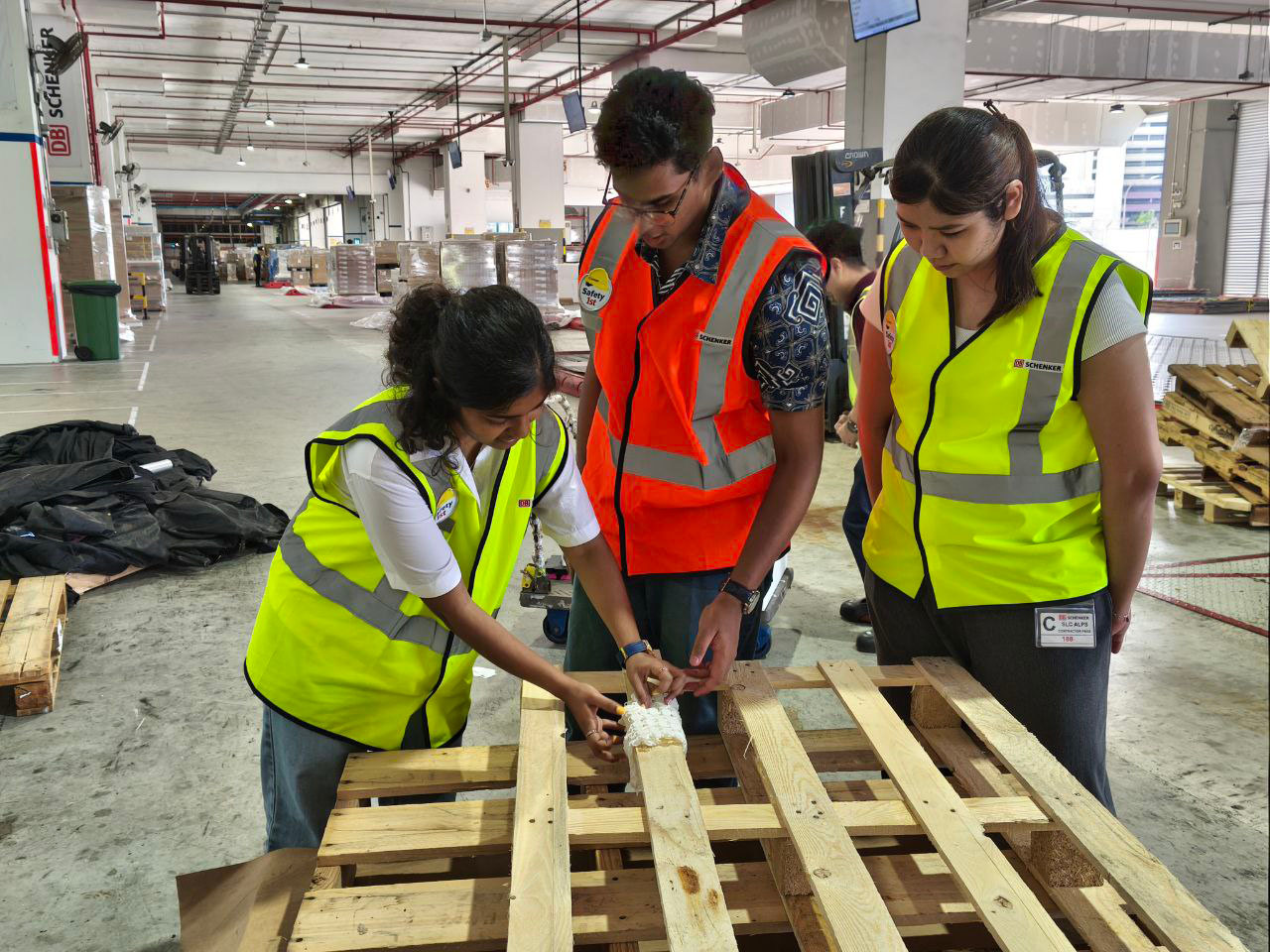
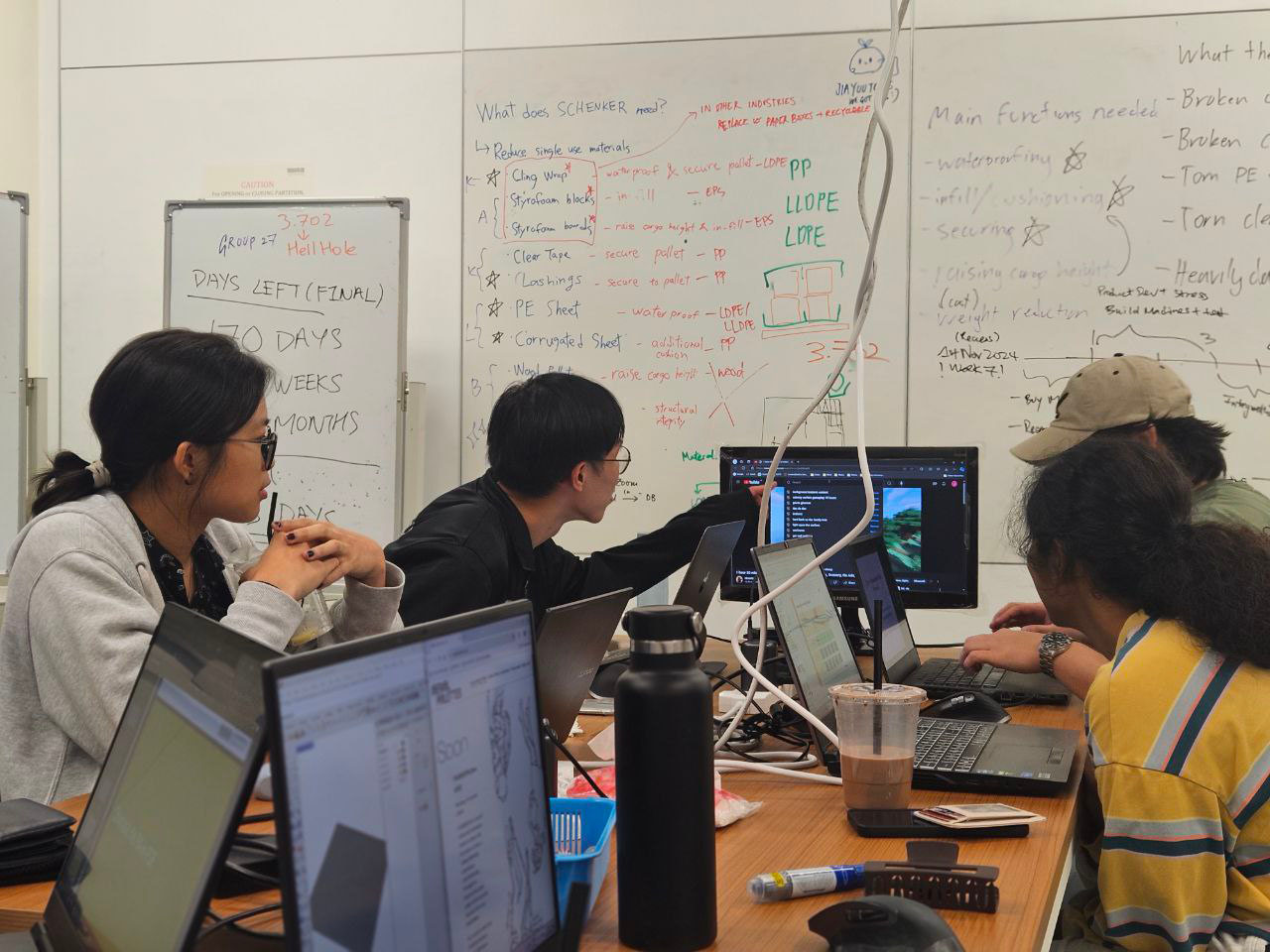