The healthcare industry faces problems in manpower shortage and logistical challenges in delivery tasks, which places a burden on its staff.
Our project reimagines hospital deliveries by introducing an autonomous robotic delivery system equipped with decentralised base stations.
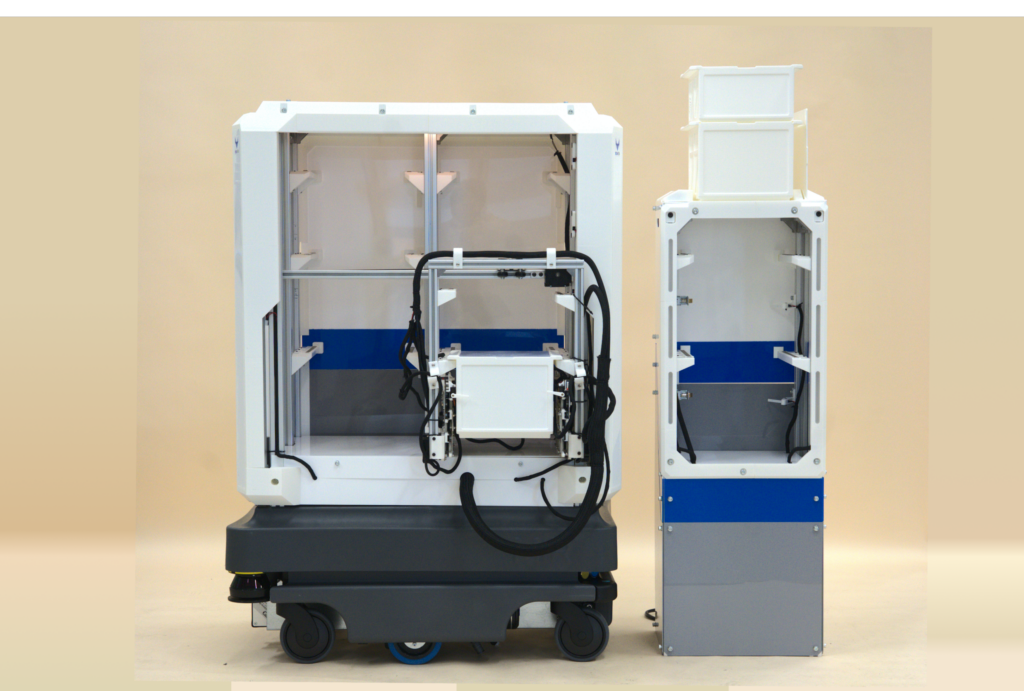
Unlike conventional systems that require hospital staff to wait for and be present when robots arrive- causing unnecessary delays and workflow disruptions, our solution allows users to drop off and collect items at smart Base Stations at their convenience.
The robot navigates independently between these stations, enabling seamless, autonomous cross-departmental transfers of essential goods via a Top Unit that autonomously handles container movement.
minimising human error • reducing workflow interruptions • increasing operational efficiency
KEY FEATURES
Automated Load and Unload
Robot handles container pickup and drop-off with minimal human input.
Task Prioritisation
Dynamic queue system ensures urgent tasks are completed first.
Secure Access Control
RFID-protected lockers allow access only to authorised users.
Versatile Payload Handling
Modular containers support a wide variety of item types.
Real-Time Delivery Tracking
Live dashboard shows delivery progress and robot location.
User-Friendly Interface
Intuitive UI for booking, tracking, and receiving updates.
Top Unit
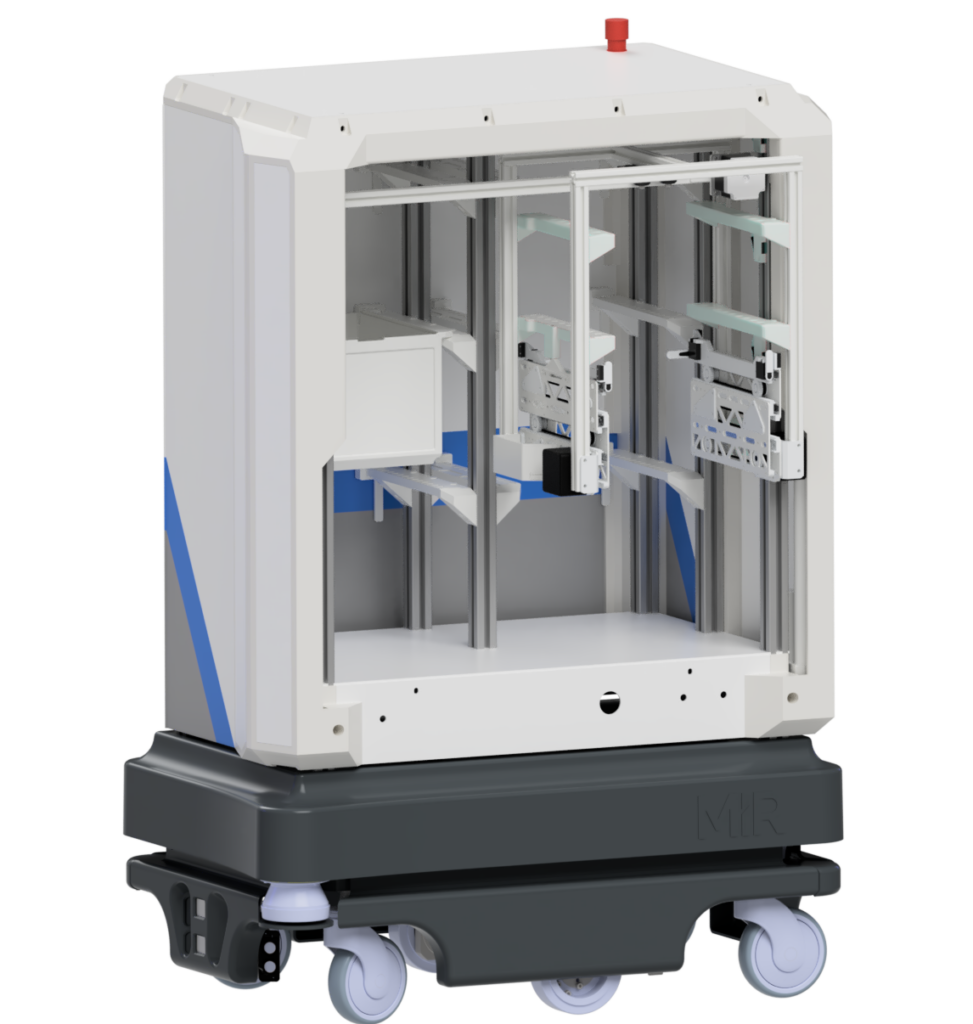
Internal storage system
for containers during
transit.
Mechanism to facilitate
the transfer of items
between Base Stations and
Top Unit
Robotic base for navigation and
movement through hospital
The Top Unit is mounted on the MiR base and handles container transfer during delivery.
It includes an internal carriage system that autonomously loads and unloads containers from base stations, storing them securely during transit.
No human interaction is needed once the delivery is scheduled.
Base Station
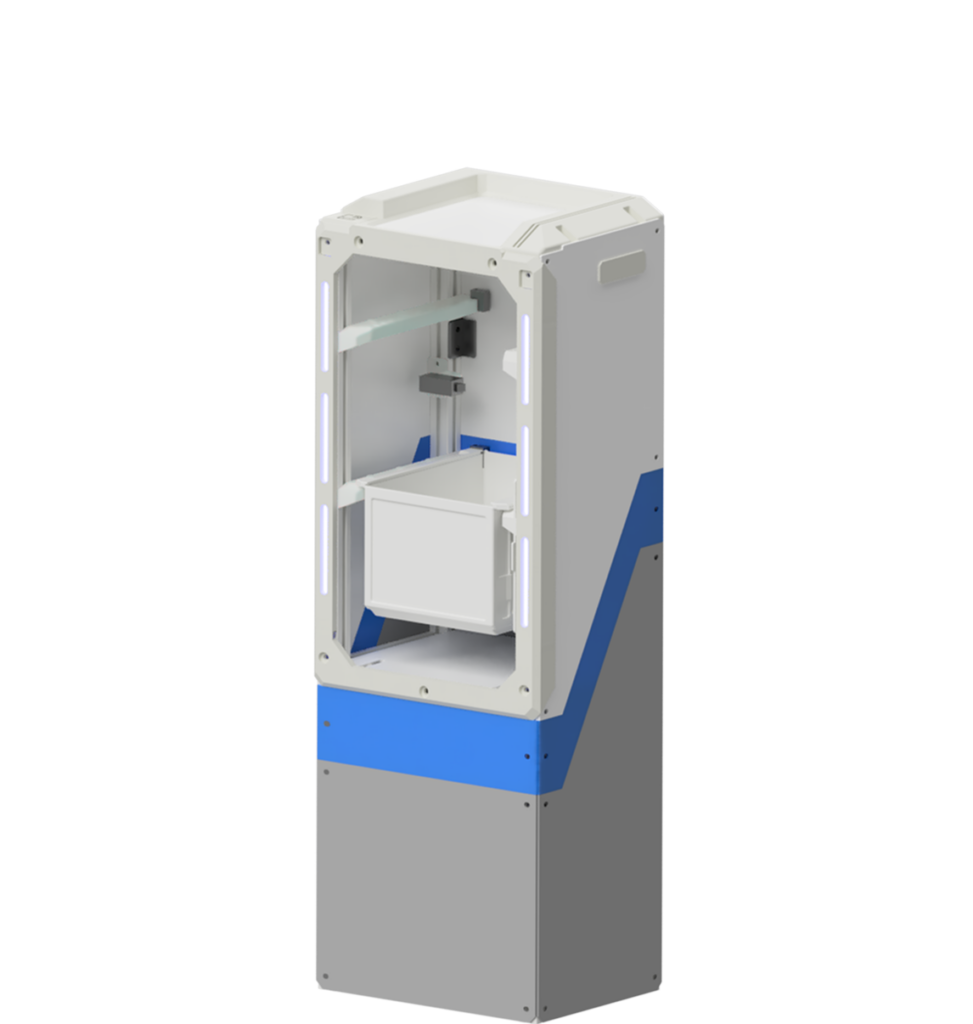
RFID Scanner for
user authentication
and security
Lock for containers
when placed in
Base Station
Container with items
for delivery locked into
Base Station
The Base Station is where items are dropped off or collected and serves as te main user interface.
Users simply scan their RFID card to access secure lockers. LED indicators guide them to the correct slot, enabling a seamless and contactless experience.
It is the intermediary of the system enabling an Automated Storage and Retrieval System flow.
Robot Dashboard
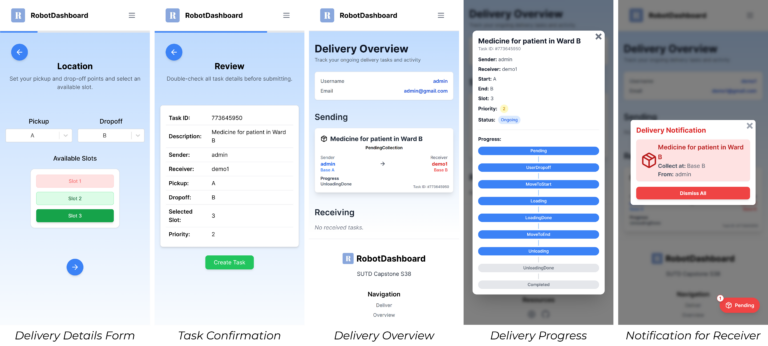
The dashboard is the command centre for users- designed for simplicity and clarity. Staff can book deliveries, set pickup/drop-off locations, and receive real-time status updates, all from one intuitive interface.
How it works
Step 1
Delivery Request
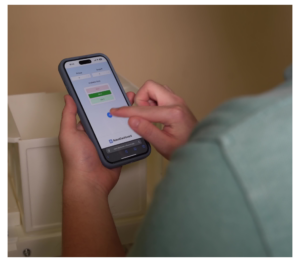
User initiates a delivery via the Robot Dashboard
Step 2
Load Item
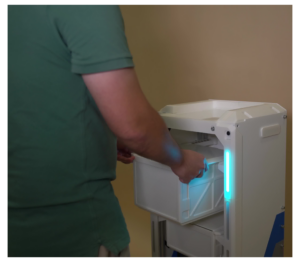
User places the item into a designated container at the Base Station
Step 3
Robot Delivery
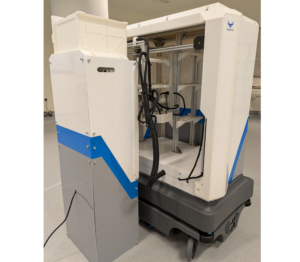
The robot autonomously navigates to the Base Station, retrieves the item, and begins delivery
Step 4
Receive Notification
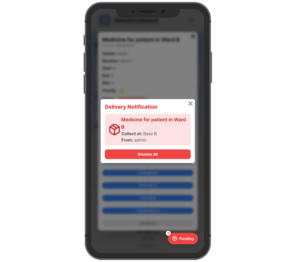
Recipient is notified when the item arrives at the destination Base Station
Step 5
Unload Item
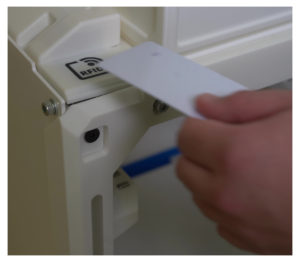
Recipient collects the item from the container at the Base Station at their convenience
Step 6
Confirm Delivery
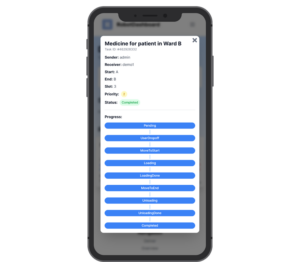
User confirms successful delivery through the Robot Dashboard
Acknowledgments
We would like to extend our heartfelt appreciation to all those who supported and contributed to the success of this project.
First and foremost, we are grateful to our partner company, Techfox, for the opportunity to collaborate on this project, and to our industry mentors, Wanjing and Sheryl, for their invaluable insights, support, and guidance throughout the process.
Our sincere thanks also go to Dr. Dileepa for his mentorship and support during our capstone journey. We would also like to acknowledge the Capstone Office for their coordination efforts and for facilitating a valuable learning experience through this programme.
We are especially thankful to our mentors from the Center for Writing and Rhetoric (CWR), Dr. Bernard and Ms. Rashmi, for their continued guidance and constructive feedback in helping us communicate our ideas clearly and effectively.
Finally, we would like to thank the FabLab staff for their technical assistance and unwavering support in the development and implementation of our project.