Final Design
Anatomy Assemble offers medical students the best of both worlds – the realistic, physical sensation of plastic models and cadavers, and the information storage potential of digital models.
Immersive Experience
Anatomy Assemble looks and feels almost like a real brain.
Independent Interaction
Anatomy Assemble can be disassembled. Each part is powered by a rechargeable battery such that it can be used on its own.
Interactive Learning
Anatomy Assemble responds to your touch, telling you the names of brain parts.
PLA Shell
The outer shell of Anatomy Assemble is 3D-printed with polylactic acid (PLA). Due to the use of magnetic resonance imaging (MRI) of a real human brain, the surface of Anatomy Assemble is anatomically accurate, with well-defined details such as the various gyri and sulci on the lobes. The close visual similarity to a real brain helps students to mentally associate what they learnt from Anatomy Assemble to an actual brain, creating an immersive experience.
Anatomy Assemble can also be taken apart into its various parts, assisting students with spatial orientation. Each part has cylindrical pins that connect and hold them together securely when assembled.
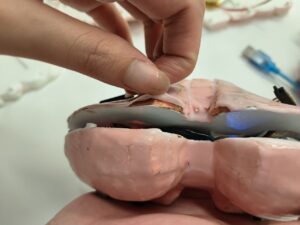
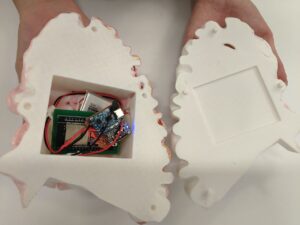
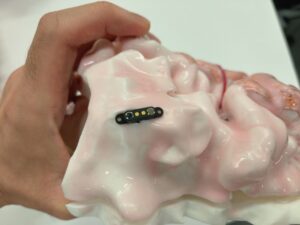
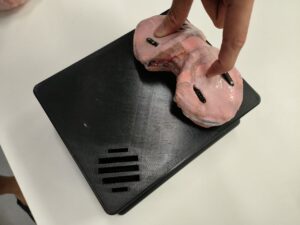
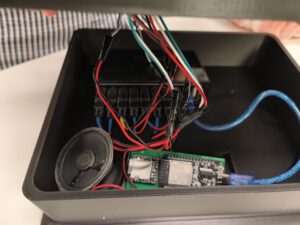
Touch-Audio System
The touch sensors on Anatomy Assemble’s surface enables interactive learning. These sensors are electrically-conductive copper tapes adhered onto the surface of Anatomy Assemble, and they are wired to an ESP32 microcontroller on the inside of each detachable brain part (known as a “Sender”). When students touch a section of the part, the sensors register the touch signal and sends it to the Sender. The Sender identifies the correct name of the section that was touched and gathers it into a data packet, before wirelessly transmitting it to another ESP32 in the charging stand (known as a “Receiver”). The Receiver then reads the data packet and identifies the correct audio file to play, then searches through an SD card for the corresponding audio file and activates the speaker to play the file, reciting the name out loud.
Within each part there is a 3.7V Li-ion rechargeable battery that powers it, enabling independent interaction as each individual part can be detached and used on its own. When assembled together, the electronics across the different parts are connected via pogo pins, allowing electrical power to be channeled throughout Anatomy Assemble when it is docked on the charging stand, ensuring that all independent parts are properly charged.
Silicone Top Layer
The exterior of Anatomy Assemble is coated with a thin layer of Smooth-Sil^TM 940 silicone. When cured, the silicone has a soft, rubbery texture that is translucent, making it the perfect material to imitate the brain tissue. Applying the silicone layer makes Anatomy Assemble feel less like a plastic model and more like a real brain, providing students with an immersive experience upon touch.
Additionally, the silicone layer protects the copper touch sensors beneath it.
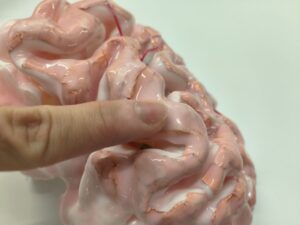

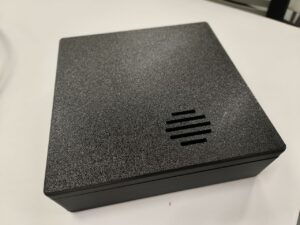
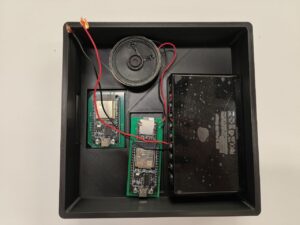
Transfer Kit
One of the suggestions for improvement brought up during the user testing was to make the electronics transferable to other models. Taking the suggestion into consideration, we came up with the transfer kit. This is a compact box that contains only the most critical components of the electronic network (one rechargeable battery, one Sender, one Receiver, one micro SD card, one speaker, and some wires with copper tape sensors at their ends). This light electronics kit allows lecturers to rapidly reconfigure a static physical model into an interactive one, enabling flexibility in teaching.
User Testing & Reviews
In the later prototyping stages, we conducted user testing to get feedback for our prototype from our target audience, LKCMedicine students. Here are our findings:



This is what they have to say about Anatomy Assemble: